Thingiverse

Filament Splice Helper - splicer by OnTheGulf
by Thingiverse
Last crawled date: 3 years ago
This is a bench splicer or in situ splicer for Anet A8.
It is a rework of TrustFm's "Filament Splicer Joiner":https://www.thingiverse.com/thing:977156/#files
The head of the TrustFm's FSJ was used and placed in a C bracket. Make sure to have some M3 nuts and bolts.
The two photos above show the splice helper used on the bench with solvent welding and in situ at the printhead of an Anet A8 for heat welding.
Solvent welding with methylene chloride works, two minute set time and half hour minimum cure time. A bit fussy but it works. $9 gets you a quart of Jasco Premium Paint & Epoxy Remover at the hardware store, it's mostly MeCl2. Here's the MSDS:
http://www.jasco-help.com/uploads/documents/GJBP00203_SDS-4015.34E.pdf
Otherwise, for heat welding, I put aluminum foil on the tip of my soldering iron, set it to 650, and very carefully sculpt a weld. This is a lot faster than solvent welding. I say sculpt because the finished weld must not be wider than the filament and cannot be too narrow or the filament will hang in the wheel and gear and not feed. Any bulge can hang up on the guide hole to the gear and wheel and the spice will break or the gear wheel will grind the filament down and the splice will not move through the hole.
Thanks again to TrustFm's head design! Again, make sure to have 2 M3 nuts and bolts, at least 6mm long, to put in the head. The nuts fit snugly and make sure the hole is cleaned out to dimension, I used an eyeglass flat screwdriver to scrape off the excess filament fluff around, in, down, and at the bottom of the hole.
I really want an in situ splicer at the print head. The difficulty is the filament wants to bend and the two pieces do not want to meet up. You might want to try TrustFm's technique also, it does overcomes the bending problem, and it uses a heat weld.
It is a rework of TrustFm's "Filament Splicer Joiner":https://www.thingiverse.com/thing:977156/#files
The head of the TrustFm's FSJ was used and placed in a C bracket. Make sure to have some M3 nuts and bolts.
The two photos above show the splice helper used on the bench with solvent welding and in situ at the printhead of an Anet A8 for heat welding.
Solvent welding with methylene chloride works, two minute set time and half hour minimum cure time. A bit fussy but it works. $9 gets you a quart of Jasco Premium Paint & Epoxy Remover at the hardware store, it's mostly MeCl2. Here's the MSDS:
http://www.jasco-help.com/uploads/documents/GJBP00203_SDS-4015.34E.pdf
Otherwise, for heat welding, I put aluminum foil on the tip of my soldering iron, set it to 650, and very carefully sculpt a weld. This is a lot faster than solvent welding. I say sculpt because the finished weld must not be wider than the filament and cannot be too narrow or the filament will hang in the wheel and gear and not feed. Any bulge can hang up on the guide hole to the gear and wheel and the spice will break or the gear wheel will grind the filament down and the splice will not move through the hole.
Thanks again to TrustFm's head design! Again, make sure to have 2 M3 nuts and bolts, at least 6mm long, to put in the head. The nuts fit snugly and make sure the hole is cleaned out to dimension, I used an eyeglass flat screwdriver to scrape off the excess filament fluff around, in, down, and at the bottom of the hole.
I really want an in situ splicer at the print head. The difficulty is the filament wants to bend and the two pieces do not want to meet up. You might want to try TrustFm's technique also, it does overcomes the bending problem, and it uses a heat weld.
Similar models
thingiverse
free

Mounted Filament Splicer
...mounted filament splicer
thingiverse
a filament splicer that i designed that uses heat from a candle to splice your filaments.
thingiverse
free

Filament Splicer by pick013
...the fillet.
video link courtsey of greendothttps://www.thingiverse.com/greendot/abouthttps://www.youtube.com/watch?v=hecs7q0hdlc
thingiverse
free

Anet A8 filament wheel by Leoallen
...i designed this for hatchbox filaments, but it will work with any filament with a hole 50-65mm (2.1-2.5in). requires two wheels.
thingiverse
free

Ultrasonic filament splicer by Terminus
...ultrasonic filament splicer by terminus
thingiverse
ultrasonic welding is the way to splice this stuff...
thingiverse
free

Anet A8 modification for filament loader (with heat sink) by lobo_tic
...e heat sink central hole, i have slightly modified the clamping part and the cover to keep using it.
https://youtu.be/resvsqighbq
thingiverse
free
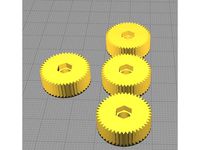
Nut support Anet a8 by Krownixs
...nut support anet a8 by krownixs
thingiverse
support of nut for the heating bed of the anet a8
thingiverse
free

Anet A8 Plus Filament Guide
...filament guide for the anet a8 plus 3d printer and maybe for other printers too. you just need two screws and t-nuts to mount it.
thingiverse
free

Ice filament wheel for anet a8 by wipolywe
...ice filament wheel for anet a8 by wipolywe
thingiverse
these are supports for ice brand filaments on my anet a8
thingiverse
free
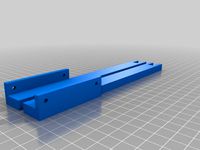
anet A8 FILAMENT HOLDER by Sois
...et a8 filament holder that is string and does not move or bend after installment. it is mounted on the back of the display board
thingiverse
free

A8 Anet base for Universal stand-alone filament spool holder by ejbantz
...t to tweak it some more:https://www.tinkercad.com/things/ieqoj77o5qs-a8-anet-base-for-universal-stand-alone-filament-spool-holder
Onthegulf
thingiverse
free
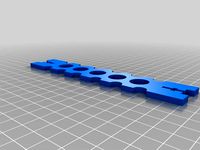
ANET A8 Spool Strut 160 mm by OnTheGulf
...dded stress relief holes and scallops to reduce print warpage.
a two up gcode file is included in the downloads to get you going.
thingiverse
free

Meade ETX-60 Telescope Rear Port Cap by OnTheGulf
...hoto. just make sure it dries overnight, the paint will flake off screwing it on, that's better than sticking from wet paint.
thingiverse
free

ANET A8 120V Power Cable Wire Clamp for stress relief by OnTheGulf
...into the clamp opening. make sure to have slack on the cable from the clamp to the power supply.
screw in the second bolt. done!
thingiverse
free
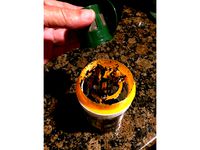
K-Cup Coffee Compost Collector on Peanut Butter Jar Lid by OnTheGulf
...o create this quickly from the work of 3dmigos and dbibeau. thanks very much for posting your work to thingiverse! credit others!
Splicer
3d_export
$5

square stainless steel glass clamp 6 9mm
...stainless steel glass clamp with flat bottom for fixing splicer lenses (6 to 9 mm), this product has an...
thingiverse
free
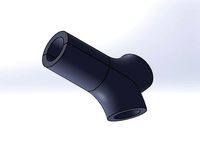
The Faucet Splicer by pegmis
...the faucet splicer by pegmis
thingiverse
the faucet splicer is used to divide one stream of water into two sinks.
thingiverse
free

Mounted Filament Splicer
...mounted filament splicer
thingiverse
a filament splicer that i designed that uses heat from a candle to splice your filaments.
thingiverse
free
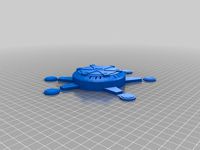
deathstorms quantum splicer by thunderbird1
...deathstorms quantum splicer by thunderbird1
thingiverse
firestorms evil doppelgangers quantum splicer
thingiverse
free
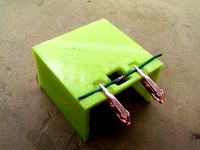
WIRE SPLICER JIG by hlyman
...er jig by hlyman
thingiverse
this wire splicer jig is a simple assembly to make and is easy and fast for joining wires together.
thingiverse
free

Splicer Bird Mask from Bioshock
... i extracted it directly from the game and smoothed it.
that was hard but you can see my cosplay of a splicer a few months ago :)
thingiverse
free
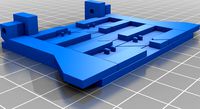
Universal 8mm film splicer by Fr3D2
... film splicer by fr3d2
thingiverse
8mm and super8 film splicer
assemble with m3 screws
printed with pla
0.2 mm layers
no support
thingiverse
free

Fixed Cooling Tray for Fujikura 70S Fusion Splicer
...ngiverse
an allways mounted cooling tray for fujikura 70s fusion splicer.
splicer do fit in transport box with the tray mounted.
thingiverse
free
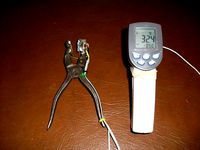
Splicer MK2 for PLA filament by Malcolm
... tool is an improvement on my previous version and is now more portable and capable of splicing long lengths of 3mm pla filament.
thingiverse
free

Ultrasonic filament splicer by Terminus
...ultrasonic filament splicer by terminus
thingiverse
ultrasonic welding is the way to splice this stuff...
Splice
3ddd
$1

"Splice" table and chairs
..."splice" table and chairs
3ddd
splice
комплект мебели из стола и 6 стульев
turbosquid
$90

SMT automatic splice tape
... available on turbo squid, the world's leading provider of digital 3d models for visualization, films, television, and games.
3ddd
$1

Splice Stool,Table,Bar Stool
... барный
набор мебели для бара, паба, дома.угловые формы придают индустриальный вид.
материал-березовая фанера.
3dfindit
free

Splices
...splices
3dfind.it
catalog: te connectivity
3dfindit
free

Junction Splices
...junction splices
3dfind.it
catalog: te connectivity
thingiverse
free

Cable Splices for BlueROV by thegwa
...cable splices for bluerov by thegwa
thingiverse
cable splices for bluerov
thingiverse
free

Tyrannosaurus splicing toys
...plicing toys
thingiverse
this toy design by ime3d
it have a splicing toys library
i use it teach 3~5 age kids what is dinosaur .
thingiverse
free

Rope Splicing Fid plk.nz by mukiwa
...rope splicing fid plk.nz by mukiwa
thingiverse
fid, rope splicing
thingiverse
free

Rope Splicing Fid plk.nz by mukiwa
...rope splicing fid plk.nz by mukiwa
thingiverse
fid, rope splicing
thingiverse
free

Rope Splicing Fid plk.nz by mukiwa
...rope splicing fid plk.nz by mukiwa
thingiverse
fid, rope splicing
Helper
turbosquid
$3
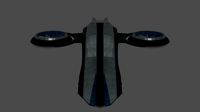
Helper Drone
...del helper drone for download as blend, blend, blend, and fbx on turbosquid: 3d models for games, architecture, videos. (1531142)
turbosquid
$10
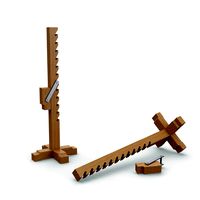
Workbench Helper
... workbench helper for download as 3ds, obj, fbx, 3dm, and skp on turbosquid: 3d models for games, architecture, videos. (1411448)
turbosquid
$39
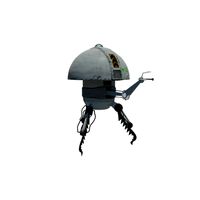
Helper 1 robot
... available on turbo squid, the world's leading provider of digital 3d models for visualization, films, television, and games.
turbosquid
$30
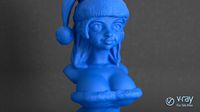
Santa Helper 3d Printable
...er 3d printable for download as max, obj, blend, stl, and ztl on turbosquid: 3d models for games, architecture, videos. (1472944)
turbosquid
free
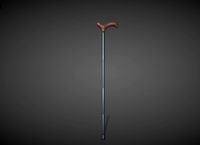
Folding sticks walking helper
...lper for download as 3ds, obj, fbx, blend, dae, stl, and gltf on turbosquid: 3d models for games, architecture, videos. (1353089)
3d_export
free
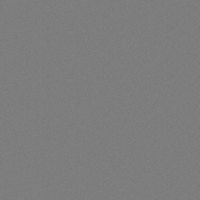
Download free UV Tile Placement Helper 2048x2048 3D Model
...s max maya uv map tile checkered checker tools utility texture
uv tile placement helper 2048x2048 3d model timb120 63561 3dexport
turbosquid
$16
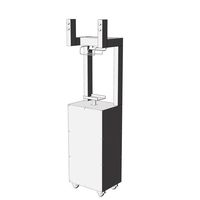
(Project) Food packing helper machine with holding clamp and press table driven by an actuator
... available on turbo squid, the world's leading provider of digital 3d models for visualization, films, television, and games.
3d_export
$8

decor-08
...elements, no groups / linked objects no lights, cameras, helper, layers, particle...
3ddd
$1
![Generic Interior Doors [Hinged]](/t/701005.jpg)
Generic Interior Doors [Hinged]
...and then you can wire the door to the helper. ...
3d_export
$5

armchair fast ikea
...totals: objects: 18 shapes: 0 cameras: 0 lights: 1 helper: 0 space warps: 0 total: 19 mesh totals: verts:...
Filament
3ddd
$1
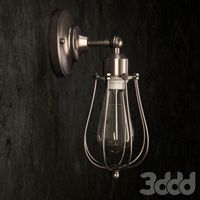
Filament Cage
...filament cage
3ddd
лофт , filament cage
модель бра, делалась по фото!
turbosquid
$3
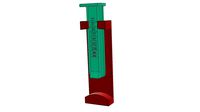
FILAMENT COUNTER
...d
royalty free 3d model filament counter for download as stl on turbosquid: 3d models for games, architecture, videos. (1563049)
3d_export
$5
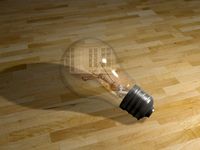
Filament lamp 3D Model
...filament lamp 3d model
3dexport
filament lamp 3d model kevin 54161 3dexport
3d_export
$5
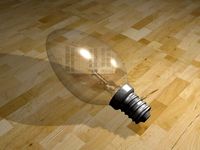
Filament bulb candle 3D Model
...filament bulb candle 3d model
3dexport
filament bulb-candle
filament bulb candle 3d model kevin 54163 3dexport
3d_export
$5

Filament led light bulb
...filament led light bulb
3dexport
realistic 3d model of filament light bulb with v-ray materials.
3d_export
$5

Filament led light bulb
...filament led light bulb
3dexport
realistic 3d model of filament light bulb with v-ray materials.
3d_export
$5

Filament led light bulb
...filament led light bulb
3dexport
realistic 3d model of filament light bulb with v-ray materials.
3d_export
$5
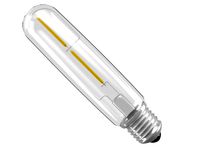
Filament led light bulb
...filament led light bulb
3dexport
realistic 3d model of filament light bulb with v-ray materials.
3d_export
$5

Filament led light bulb
...filament led light bulb
3dexport
realistic 3d model of filament light bulb with v-ray materials.
3ddd
$1
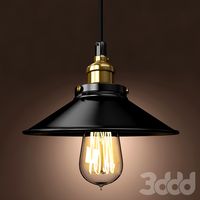
Factory filament metal shade
...factory filament metal shade
3ddd
restoration hardware
restoration hardware. 20th c. factory filament metal shade.