Thingiverse
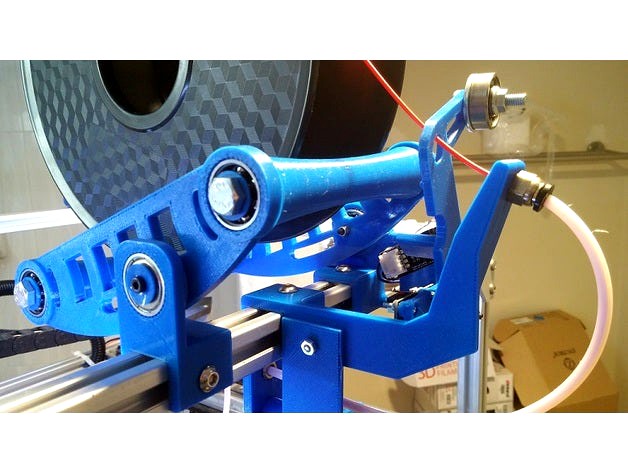
Even More Reliable Filament Runout Sensor and Spool Holder by bwaslo
by Thingiverse
Last crawled date: 3 years ago
This version is operatonally derived from my earlier "Reliable Filament Runout Sensor" (https://www.thingiverse.com/thing:2483919) from last year. Both versions are designed to mount on a 2020 bar which can be part of the printer or part of a separate filament holder. The first design works very reliably when filament runs out and the end of it comes free from the spool. BUT -- there are times when the filament is taped to or bent through an inaccessible hole in the spool so that it can't easily come free. Then the filament doesn't get pulled through the trip sensor. It doesn't happen often, but can be kind of disastrous when it does. Like, when you already have more than a dozen hours into making a big print and then the filament stops flowing as the printer thinks it is still printing and keeps going. One time while I was watching, it pulled the spool right off its rollers (which inspired the tension sensing method for this second version).
So, this version still works (for freely flowing filament) by using a gravity-powered trip arm that is held up by filament (when filament runs out, the arm falls and trips a switch). But this design adds another sensor that activates on high filament tension. Should the filament grab at the end of a spool (or even before), the spool is tugged forward. But the spool holder now can tip on bearings (the 608 skate bearings you still have -- admit it! -- from building in the fidget spinner craze) so that the holder tips forward and taps a mechanical microswitch when filament tension to the spool gets high. Both sensors are mechanical switches now (the standard microswitch end-stop boards, https://folgertech.com/collections/sensors-and-modules/products/end-stop), as they are less expensive and don't have problems with IR light not getting blocked well by some plastic parts, very non-fussy.
The tipping spool holder scheme works quite well as tipping requires less force as the spool empties. The gravity trip arm sensor is balanced (using yet another 608 bearing as a weight) so that the filament feels very little tug from the arm, but once it does run out, the weight goes out of balance and pushes the microswitch with good force. One of the screws mounting the microswitch boards should be longer, to feed through the curved slot in the lever arm. This is to keep the balanced arm from being able to tip the wrong way.
The setup ideally feeds the filament through a "reverse bowden" tube (though it doesn't have to) which completely prevents filament from ever spilling over the edge of the spool --strongly recommended if you have a direct-feed extruder. Either way, use two PC4-M10 Bowden tube bolt-on connectors (Amazon or Aliexpress) to hold and feed the 4mm (2mm internal) PTFE tubing used to guide the filament from the opening of the gravity-trip arm to the printer or other frame. The tube can extend all the way to the extruder for a "reverse bowden".
The spool holder is wide enough to hold any spools up to several kg, without needing any adjustments Spools are simply set on top of the curved rollers-- no rods to feed through, no holder width to adjust, fast and easy to change spools. The spool holder rolllers are tapered (narrower toward center) so that the spool tends to center, helping alignment with the gravity-trip arm. You'll need two 1/4" x 5.5" (or metric equivalent) and nuts to put through the spool holder rollers. Don't be tempted to use lightweight bolts, as (at least at the back) the weight of the bolt is needed to keep the structure from tipping too easily.
The photos show other plastic pieces that were put together for mounting a webcam (on my printer -- an FT-5 -- it turned out to be in the right placement for monitoring printing via Octopi). I didn't include STLs for those parts as they are a different function and would depend on printer and camera types.
[Edit Sept 2018: I managed to break my center guide when a blob on the filament caught in the PTFE tube and I tried to yank it out from the spool end. Since I needed to print a new one, I also strengthened the piece to prevent breaking should I do something dumb like that again. The new piece also has a place for a second PC4-M10, for looping the tube around like I have in the pictures -- I'd recommend using the on named "Center_Guide_redone" rather than "Center_Guide_old...."]
Attached also is a drawing for how to wire the end stop boards, along with code changes for Marlin so that it can use the sensors and do it's cool alarm, pause, and wait for filament change trick. You'll need 8 608 skate bearings, use the smoothest rolling ones for the spool rollers, and the least rolly one of course for the balance weight.
So, this version still works (for freely flowing filament) by using a gravity-powered trip arm that is held up by filament (when filament runs out, the arm falls and trips a switch). But this design adds another sensor that activates on high filament tension. Should the filament grab at the end of a spool (or even before), the spool is tugged forward. But the spool holder now can tip on bearings (the 608 skate bearings you still have -- admit it! -- from building in the fidget spinner craze) so that the holder tips forward and taps a mechanical microswitch when filament tension to the spool gets high. Both sensors are mechanical switches now (the standard microswitch end-stop boards, https://folgertech.com/collections/sensors-and-modules/products/end-stop), as they are less expensive and don't have problems with IR light not getting blocked well by some plastic parts, very non-fussy.
The tipping spool holder scheme works quite well as tipping requires less force as the spool empties. The gravity trip arm sensor is balanced (using yet another 608 bearing as a weight) so that the filament feels very little tug from the arm, but once it does run out, the weight goes out of balance and pushes the microswitch with good force. One of the screws mounting the microswitch boards should be longer, to feed through the curved slot in the lever arm. This is to keep the balanced arm from being able to tip the wrong way.
The setup ideally feeds the filament through a "reverse bowden" tube (though it doesn't have to) which completely prevents filament from ever spilling over the edge of the spool --strongly recommended if you have a direct-feed extruder. Either way, use two PC4-M10 Bowden tube bolt-on connectors (Amazon or Aliexpress) to hold and feed the 4mm (2mm internal) PTFE tubing used to guide the filament from the opening of the gravity-trip arm to the printer or other frame. The tube can extend all the way to the extruder for a "reverse bowden".
The spool holder is wide enough to hold any spools up to several kg, without needing any adjustments Spools are simply set on top of the curved rollers-- no rods to feed through, no holder width to adjust, fast and easy to change spools. The spool holder rolllers are tapered (narrower toward center) so that the spool tends to center, helping alignment with the gravity-trip arm. You'll need two 1/4" x 5.5" (or metric equivalent) and nuts to put through the spool holder rollers. Don't be tempted to use lightweight bolts, as (at least at the back) the weight of the bolt is needed to keep the structure from tipping too easily.
The photos show other plastic pieces that were put together for mounting a webcam (on my printer -- an FT-5 -- it turned out to be in the right placement for monitoring printing via Octopi). I didn't include STLs for those parts as they are a different function and would depend on printer and camera types.
[Edit Sept 2018: I managed to break my center guide when a blob on the filament caught in the PTFE tube and I tried to yank it out from the spool end. Since I needed to print a new one, I also strengthened the piece to prevent breaking should I do something dumb like that again. The new piece also has a place for a second PC4-M10, for looping the tube around like I have in the pictures -- I'd recommend using the on named "Center_Guide_redone" rather than "Center_Guide_old...."]
Attached also is a drawing for how to wire the end stop boards, along with code changes for Marlin so that it can use the sensors and do it's cool alarm, pause, and wait for filament change trick. You'll need 8 608 skate bearings, use the smoothest rolling ones for the spool rollers, and the least rolly one of course for the balance weight.
Similar models
thingiverse
free
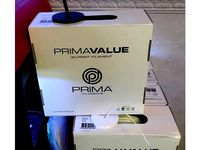
Filament guide by halixir
...ows the filament to be drawn as needed, while the weight of the spool itself keeps enough friction to stop the spool unravelling.
thingiverse
free

Lack Enclosure hanging spool holder
...the holder, plus a mirror image, and the roller which is from the filler spool holder. roller requires 2 608 skateboard bearings.
thingiverse
free

Filament tube holder with alarm by johnsvensk
...ent, and an arduino (adafruit trinket) that for now only produces a square wave signal for the buzzer when the spool is empty ...
thingiverse
free

72mm 608 bearing tube for filament spool by msenese
... for the printrbot play (file: https://www.thingiverse.com/thing:1161647) and it works great. only needs 2 bearings instead of 8.
thingiverse
free
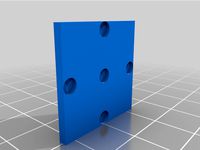
Filament Roller and Spool holder by Vardamanj
...se
i wanted to mount my spool inside my cabinet and rollers are to guide the filament around the top then feed into the printer.
thingiverse
free

filament spool holder by jimshady
... keep the spool from moving side to side no support is needed as i made a way to reduce filament use and still not need support.
thingiverse
free

Filament Spool for Small Filament Amounts by Grim_Havok
...g' back on themselves, so i added some to this design.
this isn't my best print ever, but it was functional so i kept it.
thingiverse
free

Filament Roller Support by southbaygsr
...t;roller" that doesn't spin that matches the supports. without bearings, a 1kg spool is dispensed at a reasonable rate.
thingiverse
free

Filament Out Side On Sensor box Microswitch version by ProtomakerSprint
...ideo 3d printout and test. testing filament run out begins at : 23:26
filament out side on sensor boxhttps://youtu.be/ojtsy-2ukde
thingiverse
free

TronXY XY-2 Pro Spool Roller
...ge end in to old in place. arms on the base keep the spool from sliding off.
you will need to print 2 rollers, and 1 base.
enjoy!
Bwaslo
thingiverse
free
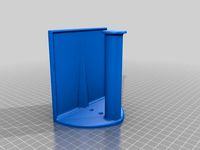
Another tp holder by bwaslo
...r larger paper rolls, and that also prints a little nicer (no overhands), also check outhttps://www.thingiverse.com/thing:3575916
thingiverse
free
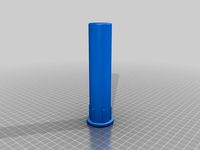
Port tube for speaker cabinet by bwaslo
...ill take quite a while and a lot of filament, though.... check my other things to see if i've posted a design for that yet...
thingiverse
free
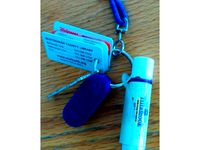
Lip Balm (Chapstick) clip by bwaslo
...ng it any harder to get in. my wife lost a chapstick from it slipping out, so i made her one that is a little tighter like that.
thingiverse
free

Short 33rpm spindle for Dual 1218 turntable by bwaslo
...70s and 80s. quick print, i used pillar supports (in slic3r pe) but it might print without. beats paying $15 for one from ebay!
thingiverse
free

Don't Panic! Button guard for LCD controller by bwaslo
...n except when you really mean to!
i plan to retire and live in luxury off the tips from this submission, so keep them rolling in!
thingiverse
free
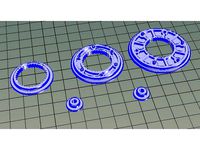
Pulleys using 608 bearings by bwaslo
... good solid piece.
i've done some in pla and in pet-g, should work ok with abs too i imagine. hope you find a use for these/
thingiverse
free
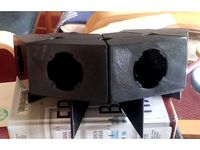
Enclosures for BMR ambient tweeters by bwaslo
...discussion, at the diyaudio.com website: http://www.diyaudio.com/forums/multi-way/326055-ambience-tweeters-using-bmr-drivers.html
thingiverse
free

Floating cup (Starbucks-remix) by cr3beast
...figured i'd share it. thank you to happymoon and bwaslo for the original and improved models that i used...
thingiverse
free

Cabinet for 2-way ported loudspeaker by bwaslo
...eason i haven't printed it yet.
if by chance anyone out there prints this (maybe for a challenge?), please post a photo here!
thingiverse
free
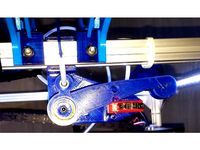
Reliable Filament Runout Sensor by bwaslo
...-optical-endstop-control-printer/dp/b01flsa47o/ref=sr_1_2?ie=utf8&qid=1502728465&sr=8-2&keywords=optical+limit+switch
Runout
3d_export
$6
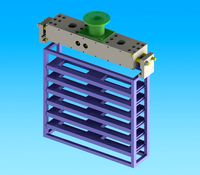
clamping mechanism of heavy workpiece
...load<br>the inertia force at the maximum acceleration of horizontal runout is less than the retraction side thrust of cylinder.<br>selection...
thingiverse
free
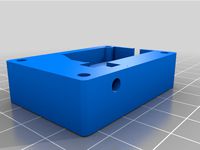
Filament runout sensor by TA1AUB
...filament runout sensor by ta1aub
thingiverse
filament runout sensor
thingiverse
free

Runout filament sensor by davidix68
...runout filament sensor by davidix68
thingiverse
ender 3 runout sensor microswitch case
thingiverse
free
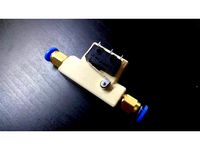
runout sensor -bowden by chroja
...runout sensor -bowden by chroja
thingiverse
runout sensor -bowden
v5 optimalize design
thingiverse
free

Filament runout sensor by jos
.../webshop/cartesio-shop/electronics/filament-runout-sensor
for assembly :http://mauk.cc/mediawiki/index.php/filament_runout_sensor
thingiverse
free

Filament runout by pochetto
...y pochetto
thingiverse
easy filament runout.
1 endstop
1 led
nel firmware attivare la funzione di fine filo e assegnare un pin.
thingiverse
free

Filament runout sensor support by 100s99s
...filament runout sensor support by 100s99s
thingiverse
support for filament runout sensor of direct drive.
thingiverse
free

Swivel mount runout sensor by notnyt
...swivel mount runout sensor by notnyt
thingiverse
608 bearing mounted filament runout sensor
thingiverse
free

Filament runout sensor fastener by Cherepok
...filament runout sensor fastener by cherepok
thingiverse
movable adjustable mount for bigtreetech filament runout sensor.
thingiverse
free

Runout gauge for pulley by tom4cad
...runout gauge for pulley by tom4cad
thingiverse
20t pulley with 5 mm bore. measured runout 0,07 mm
edit
tool with 8mm hole added
Reliable
3d_export
$95

Falcon3D MD 80 Reliable Air Cargo 3D Model
...ate mcdonnell douglas us plane planes jet jetliner md-80 md 80
falcon3d md 80 reliable air cargo 3d model falcon3d 73667 3dexport
3d_export
$5

Cross 3D Model
...cross 3d model 3dexport cross cross 3d model reliable 40331...
3d_export
$5

Silver ring 3D Model
...model 3dexport ring jewellery silver silver ring 3d model reliable 40456...
3d_export
free
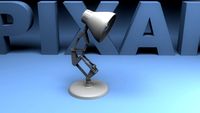
Download free Pixar Lamp 3D Model
...3d model 3dexport lamp pixar pixar lamp 3d model reliable 41625...
3d_export
$80
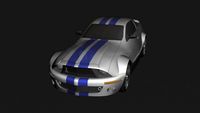
Ford Mustang GT500 3D Model
...ford mustang gt500 car ford mustang gt500 3d model reliable 40078...
3d_export
$10
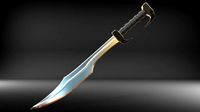
Sword From The Movie The 300 Spartans
...with high quality textures and materials in compliance with the reliability of the source type of sword. textural sweep included.
3d_export
$7

Footrest 01 3D Model
...furnish furniture wood modern spa style stylish curve strong reliable leg foot feet four footrest 01 3d model acmedesigns...
3d_export
$10
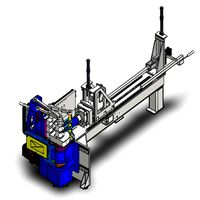
cnc automatic pipe bender
...kind of pipe feeding equipment is very reliable and reliable the equipment has several characteristics: 1. plc control, program...
3d_ocean
$35

Pzkpf I Ausf B
...introducing the six cylinder water cooled engine and more reliable gearbox. tracks are...
3d_export
$15

Air purifier Bork
...the same time, on each side there is a reliable system of preliminary and combined...
Sensor
3d_export
free

parking sensor
...parking sensor
3dexport
car parking sensor
turbosquid
$1
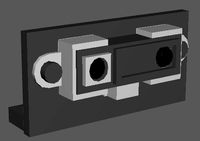
Sensor
... available on turbo squid, the world's leading provider of digital 3d models for visualization, films, television, and games.
3d_export
$5
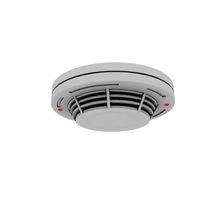
Smoke sensor
...port
smoke sensor, can be an impressive element for your projects. easy to use, realistic image, low polygon, quality materials.
3d_export
$5
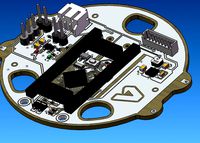
Air Quality Sensor v1
...air quality sensor v1
3dexport
air quality sensor v1
3d_export
$15
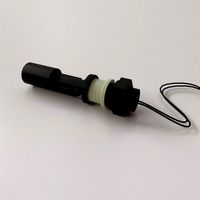
float sensor
...e up render. - all parts and materials are logically named. other formats ================= - collada (.dae) - autodesk fbx - obj
turbosquid
$26
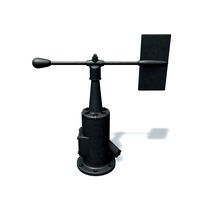
Wind sensor C
...free 3d model wind sensor c for download as 3ds, obj, and fbx on turbosquid: 3d models for games, architecture, videos. (1328943)
turbosquid
$26
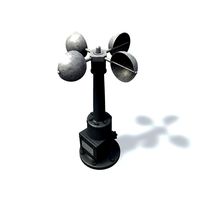
Wind sensor B
...free 3d model wind sensor b for download as 3ds, obj, and fbx on turbosquid: 3d models for games, architecture, videos. (1328168)
3d_export
$5
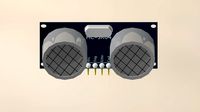
ultrasound sensor
...ivers convert ultrasound into electrical signals, and transceivers can both transmit and receive ultrasound. export in: -obj -fbx
3ddd
free
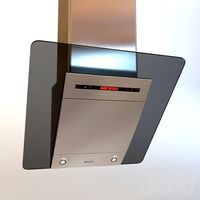
Вытяжка Shindo pallada sensor
... вытяжка
вытяжка shindo pallada sensor. в двух размерах - 600 и 900. текстуры в комплекте.
turbosquid
$52
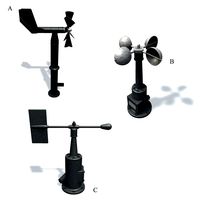
Wind sensor A B C
...
royalty free 3d model wind sensor a b c for download as fbx on turbosquid: 3d models for games, architecture, videos. (1408406)
Spool
3ddd
$1

spool c53301
...spool c53301
3ddd
spool
spool c53301 650х350х145
turbosquid
$3

Cable Spool
...royalty free 3d model cable spool for download as max and fbx on turbosquid: 3d models for games, architecture, videos. (1457009)
turbosquid
free

Pallets and Spool
... available on turbo squid, the world's leading provider of digital 3d models for visualization, films, television, and games.
turbosquid
$10

Spool of String
...ol of string pink for download as c4d, 3ds, fbx, obj, and stl on turbosquid: 3d models for games, architecture, videos. (1647892)
3ddd
$1

Подвесные светильники Spool
...ye/podvesnoy_svetilnik_spool_d320/ http://www.cosmorelax.ru/catalog/podvesnyye/podvesnoy_svetilnik_spool_d420/
3ddd
free

Spool 001 sofa
...spool 001 sofa
3ddd
roda
roda
collection spool
design rodolfo dordoni
dimensions:
lenght 90 cm
depth 94 cm
height 79 cm
turbosquid
$15
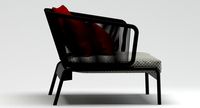
Roda Spool Sofa
...ee 3d model roda spool sofa for download as max, obj, and fbx on turbosquid: 3d models for games, architecture, videos. (1502650)
turbosquid
$95
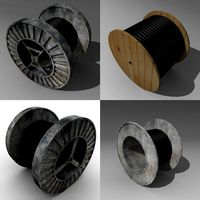
wire spools 3ds
... available on turbo squid, the world's leading provider of digital 3d models for visualization, films, television, and games.
turbosquid
$20
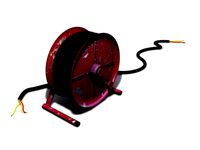
spool of TV wire
... available on turbo squid, the world's leading provider of digital 3d models for visualization, films, television, and games.
turbosquid
$3

Simple and Fast Spool Holder
...ree 3d model simple and fast spool holder for download as stl on turbosquid: 3d models for games, architecture, videos. (1548546)
Even
turbosquid
$20
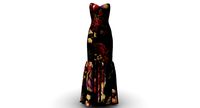
Evening Dress
...oyalty free 3d model evening dress for download as ma and obj on turbosquid: 3d models for games, architecture, videos. (1146724)
3d_export
$7

evening cafe
...evening cafe
3dexport
turbosquid
$10

Evening room
... available on turbo squid, the world's leading provider of digital 3d models for visualization, films, television, and games.
turbosquid
$10

Evening dress
... available on turbo squid, the world's leading provider of digital 3d models for visualization, films, television, and games.
3ddd
$1
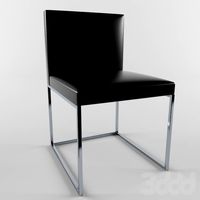
Calligaris Even Plus
...calligaris even plus
3ddd
calligaris
calligaris_chair_even plus
turbosquid
$47

Evening dress 8
... available on turbo squid, the world's leading provider of digital 3d models for visualization, films, television, and games.
turbosquid
$34

Evening dress 3
... available on turbo squid, the world's leading provider of digital 3d models for visualization, films, television, and games.
turbosquid
$34
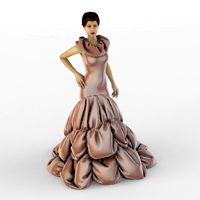
Evening dress 2
... available on turbo squid, the world's leading provider of digital 3d models for visualization, films, television, and games.
turbosquid
$34
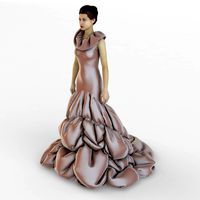
Evening dress 1
... available on turbo squid, the world's leading provider of digital 3d models for visualization, films, television, and games.
turbosquid
$11
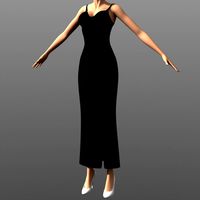
Clothing - Evening Gown
... available on turbo squid, the world's leading provider of digital 3d models for visualization, films, television, and games.
Filament
3ddd
$1
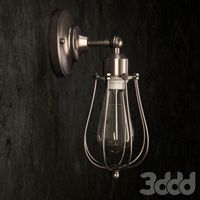
Filament Cage
...filament cage
3ddd
лофт , filament cage
модель бра, делалась по фото!
turbosquid
$3
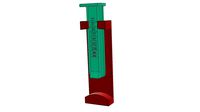
FILAMENT COUNTER
...d
royalty free 3d model filament counter for download as stl on turbosquid: 3d models for games, architecture, videos. (1563049)
3d_export
$5
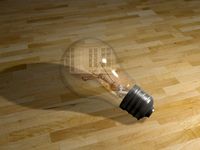
Filament lamp 3D Model
...filament lamp 3d model
3dexport
filament lamp 3d model kevin 54161 3dexport
3d_export
$5
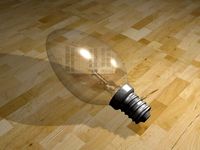
Filament bulb candle 3D Model
...filament bulb candle 3d model
3dexport
filament bulb-candle
filament bulb candle 3d model kevin 54163 3dexport
3d_export
$5

Filament led light bulb
...filament led light bulb
3dexport
realistic 3d model of filament light bulb with v-ray materials.
3d_export
$5

Filament led light bulb
...filament led light bulb
3dexport
realistic 3d model of filament light bulb with v-ray materials.
3d_export
$5

Filament led light bulb
...filament led light bulb
3dexport
realistic 3d model of filament light bulb with v-ray materials.
3d_export
$5
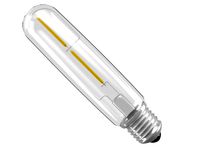
Filament led light bulb
...filament led light bulb
3dexport
realistic 3d model of filament light bulb with v-ray materials.
3d_export
$5

Filament led light bulb
...filament led light bulb
3dexport
realistic 3d model of filament light bulb with v-ray materials.
3ddd
$1
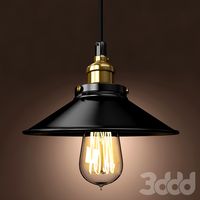
Factory filament metal shade
...factory filament metal shade
3ddd
restoration hardware
restoration hardware. 20th c. factory filament metal shade.
Holder
archibase_planet
free
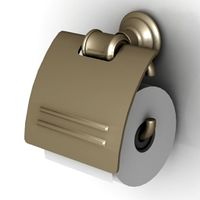
Holder
...holder
archibase planet
holder toilet paper holder
holder paper n070712 - 3d model (*.gsm+*.3ds) for interior 3d visualization.
archibase_planet
free
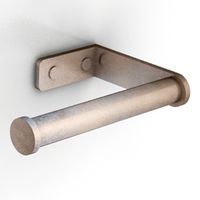
Holder
...e planet
holder rack toilet paper holder
holder toilet roll n240715 - 3d model (*.gsm+*.3ds+*.max) for interior 3d visualization.
archibase_planet
free
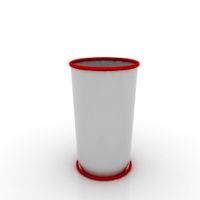
Holder
...holder
archibase planet
pen holder support prop
pen holder - 3d model for interior 3d visualization.
archibase_planet
free

Holder
...holder
archibase planet
pole post holder
сhurch cross pole holder - 3d model for interior 3d visualization.
archibase_planet
free
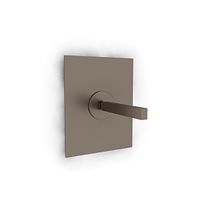
Holder
...holder
archibase planet
holder bathroom ware
shower holder - 3d model (*.gsm+*.3ds) for interior 3d visualization.
archibase_planet
free
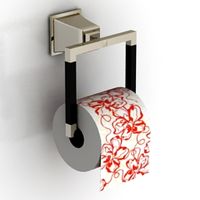
Holder
...oilet paper holder
holder paper devon&devon; time black n241113 - 3d model (*.gsm+*.3ds+*.max) for interior 3d visualization.
archibase_planet
free

Holder
...holder
archibase planet
holder hanger hanger for towel
holder 7 - 3d model (*.gsm+*.3ds) for interior 3d visualization.
archibase_planet
free
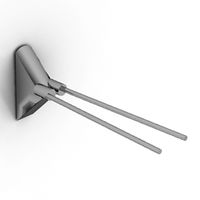
Holder
...holder
archibase planet
holder hanger hanger for towel
holder 3 - 3d model (*.gsm+*.3ds) for interior 3d visualization.
archibase_planet
free
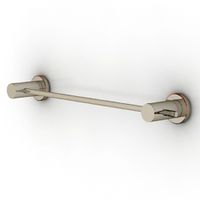
Holder
...holder
archibase planet
holder towel rack towel-horse
holder - 3d model (*.gsm+*.3ds) for interior 3d visualization.
archibase_planet
free
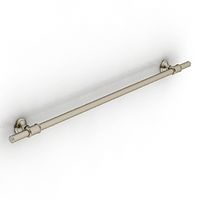
Holder
...lder
archibase planet
holder hanger hanger for towel
holder towel n250912 - 3d model (*.gsm+*.3ds) for interior 3d visualization.
More
turbosquid
$15

more
... available on turbo squid, the world's leading provider of digital 3d models for visualization, films, television, and games.
3ddd
free

more
...more
3ddd
amore , шкаф
шкаф amore abj 301
turbosquid
$49

Thomas More
...osquid
royalty free 3d model thomas more for download as fbx on turbosquid: 3d models for games, architecture, videos. (1617580)
turbosquid
$15

Visign for More
... available on turbo squid, the world's leading provider of digital 3d models for visualization, films, television, and games.
turbosquid
$15

Table - Moree
... available on turbo squid, the world's leading provider of digital 3d models for visualization, films, television, and games.
3ddd
free

Glam-More Caracole
...glam-more caracole
3ddd
glam-more , тумба
размеры: 37w x 18d x 32h
design_connected
free

The More, The Merrier Candlestick
...e merrier candlestick
designconnected
free 3d model of the more, the merrier candlestick by muuto designed by campbell, louise.
turbosquid
$27

fantasy plants and more
...d model fantasy plants and more for download as blend and obj on turbosquid: 3d models for games, architecture, videos. (1711843)
3ddd
$1
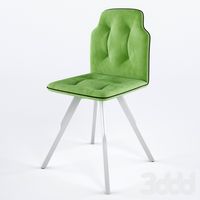
Betibu Chairs & More
...betibu chairs & more
3ddd
chairs&more
.betibu chairs & more
turbosquid
$139
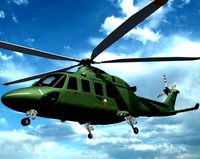
AW139(more accurate)
... available on turbo squid, the world's leading provider of digital 3d models for visualization, films, television, and games.