GrabCAD
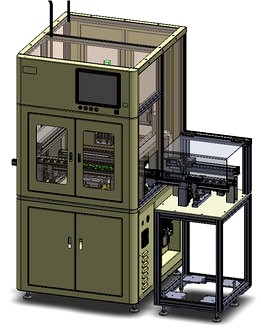
Cover Place Machine
by GrabCAD
Last crawled date: 1 year, 11 months ago
Process
The pallet containing parts is fed through a conveyor system within the Cover placement and press. The conveyor system must consist of three in-line sections for better process control. The material flow should be made flexible through a bipolar conveyor or other means (either from LEFT-to-RIGHT or RIGHT-to-LEFT)
Cycle Time
The Cover placement and pressed conveyor should be programmable for user. The Gen products require cycle time of less than 16.8 sec/pallet.
3.2 Operation Sequence
1) Once the machine is available for receiving new pallet for processing, it shall signal the previous station linked conveyor module to transfer a pallet (C1) in.
2) Once the previous machine sent the new pallet into machine, an input sensor shall “receive” the pallet. Sensors to read number of housing present on pallet, and read the pallet ID to select the model parameter (robot position) and if different model then a message prone to change model. The incoming conveyor shall transfer the pallet into the working conveyor (centre conveyor).
3) The pallet shall lift up by the commonise lifter from below. The commonise pick and place will pick up two covers from the escapement. Place them on the first pair of housing. Press is down when robot place covers on housing. At this position, height sensor checks the press is in full stroke indicate covers are place in the correct position and fully seated onto the groove, pick and place cycle continue. Height sensor fail, when it detects that the cylinder is at fully extend stroke, mean covers that are not fully seated on the groove. Alarm indication appears on touch screen and indicating the location that is/are having placement problem.
4) C3 last conveyer transfer pallet to next machine.
The pallet containing parts is fed through a conveyor system within the Cover placement and press. The conveyor system must consist of three in-line sections for better process control. The material flow should be made flexible through a bipolar conveyor or other means (either from LEFT-to-RIGHT or RIGHT-to-LEFT)
Cycle Time
The Cover placement and pressed conveyor should be programmable for user. The Gen products require cycle time of less than 16.8 sec/pallet.
3.2 Operation Sequence
1) Once the machine is available for receiving new pallet for processing, it shall signal the previous station linked conveyor module to transfer a pallet (C1) in.
2) Once the previous machine sent the new pallet into machine, an input sensor shall “receive” the pallet. Sensors to read number of housing present on pallet, and read the pallet ID to select the model parameter (robot position) and if different model then a message prone to change model. The incoming conveyor shall transfer the pallet into the working conveyor (centre conveyor).
3) The pallet shall lift up by the commonise lifter from below. The commonise pick and place will pick up two covers from the escapement. Place them on the first pair of housing. Press is down when robot place covers on housing. At this position, height sensor checks the press is in full stroke indicate covers are place in the correct position and fully seated onto the groove, pick and place cycle continue. Height sensor fail, when it detects that the cylinder is at fully extend stroke, mean covers that are not fully seated on the groove. Alarm indication appears on touch screen and indicating the location that is/are having placement problem.
4) C3 last conveyer transfer pallet to next machine.
Similar models
grabcad
free

On Pallet Pressing Machine With Conveyor
...on pallet pressing machine with conveyor
grabcad
on pallet pressing machine with conveyor
grabcad
free

Engine Transfer Conveyor
...lift down transfer at lower conveyor to the end and lift up at home position.
total pallet on conveyor systems running = 4 units.
grabcad
free

Linear High Speed Linear Converyor With Cylinder
...mbly process from bowl feeder
-pick and place (jig and fixture), pressing and auto screwing
*full design will be shared later on
cg_trader
$19
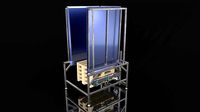
Pallet Dispenser Robot
... from the system. pallet is loaded into the machine with the help of forklift. it is applied to the existing conveyor if desired.
grabcad
free

Linear Conveyor System with Pneumatic Cylinder
...rewing
another linear conveyor with pneumatic cylidner (https://grabcad.com/library/linear-high-speed-converyor-with-cylinder-1)
grabcad
free

Pick and Place #3 - dual stroke pneumatic cylinder
..., consist of 2 pcs of pneumatic round cylinder, give ability to pick the part in deeper height and placed it into shorter height.
grabcad
free

Fix and transfer pallet by plastic chain conveyor
...fix and transfer pallet by plastic chain conveyor
grabcad
fix, stopper and transfer pallet by plastic conveyor.
grabcad
free

CONVEYOR HANDLING SYSTEM, DRILLING MOLDS
... handling system, drilling molds
grabcad
press drilling process is performed on the conveyor with the pneumatic transfer system.
grabcad
free

Pallet Dispenser Robot
...d into the machine with the help of forklift. it is applied to the existing conveyor if desired.
for cad model www.mhsmakine.com
grabcad
free

Transfer Conveyor Belt
...ace left on either side of the conveyor belt for personnel interference. the dimensions of the conveyor belt is 1,000mmm x 400mm.
Cover
archibase_planet
free
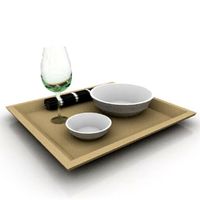
Cover
...cover
archibase planet
cover place setting
cover n170807 - 3d model for interior 3d visualization.
3ddd
$1

cover
...cover
3ddd
ковер , круглый
cover decor
archibase_planet
free
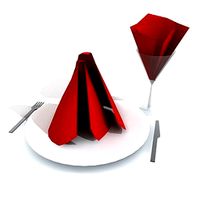
Cover
...cover
archibase planet
cover place setting setting
servis-cafe1930 - 3d model for interior 3d visualization.
turbosquid
free
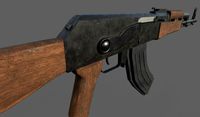
Coverings
...rings
turbosquid
free 3d model coverings for download as dwg on turbosquid: 3d models for games, architecture, videos. (1279391)
3d_export
$5

plug cover
...plug cover
3dexport
plug cover
turbosquid
$25
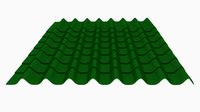
Covers
... available on turbo squid, the world's leading provider of digital 3d models for visualization, films, television, and games.
3d_export
$10
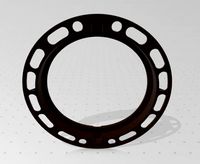
manhole cover
...manhole cover
3dexport
manhole cover gost, stl, step
turbosquid
$5

Street Gas Cover Manhole Cover
... available on turbo squid, the world's leading provider of digital 3d models for visualization, films, television, and games.
3ddd
free
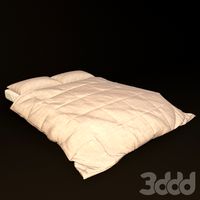
Bed cover
...bed cover
3ddd
постельное белье
very useful bed cover
3d_export
$5
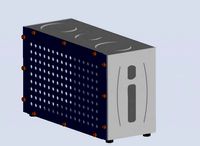
cpu cover
...cpu cover
3dexport
cpu cover, cpu box, sheet metal container
Machine
archibase_planet
free
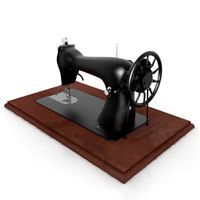
Machine
...machine
archibase planet
sewing-machine sewing machine equipment
singer machine- 3d model for interior 3d visualization.
archibase_planet
free
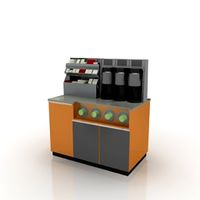
Machine
...hine
archibase planet
percolator equipment coffee-machine
machine n230708 - 3d model (*.gsm+*.3ds) for interior 3d visualization.
archibase_planet
free
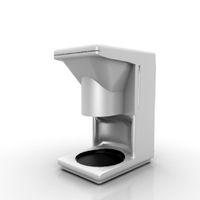
Machine
...chibase planet
percolator coffee-machine kitchen equipment
coffee machine - 3d model (*.gsm+*.3ds) for interior 3d visualization.
archibase_planet
free
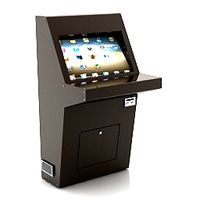
Slot machine
...ase planet
slot machine slot-machine playing machine
slot machine n260311 - 3d model (*.gsm+*.3ds) for interior 3d visualization.
turbosquid
$7

Machine
...ne
turbosquid
royalty free 3d model machine for download as on turbosquid: 3d models for games, architecture, videos. (1391792)
3d_ocean
$10
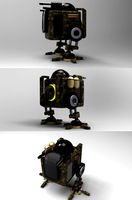
War machine
...war machine
3docean
camuflage machine robot war war machine
war machine created in 3dmax 2009 15.497-poly count
turbosquid
$7
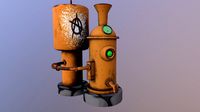
machine
...turbosquid
royalty free 3d model machine for download as obj on turbosquid: 3d models for games, architecture, videos. (1452674)
3d_ocean
$12
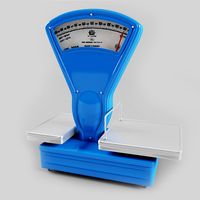
Weighing-machine
...weighing-machine
3docean
market shop weighing-machine
3d model weighing-machine
archibase_planet
free
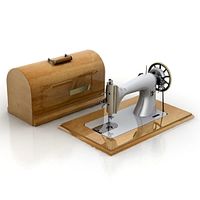
Sewing machine
...ine
archibase planet
sewing machine sewing-machine
sewing machine n080311 - 3d model (*.gsm+*.3ds) for interior 3d visualization.
archibase_planet
free
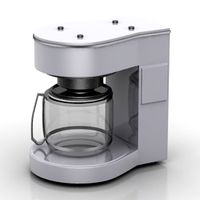
Coffee machine
...se planet
coffee machine percolator coffee-machine
coffee machine n010715 - 3d model (*.gsm+*.3ds) for interior 3d visualization.
Place
3d_ocean
$7
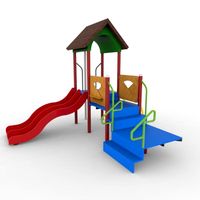
game place
...game place
3docean
children game game park game place kids play luna park play
for kids game place
3d_export
$5

seating places
...seating places
3dexport
seating places with coverage modeling by: sketch up rendering by: lumion
3d_export
$5
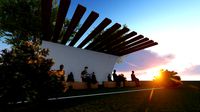
seating places
...seating places
3dexport
seating places with coverage modeling by: sketch up 2017 rendering by: lumion 6.5.1
3ddd
$1
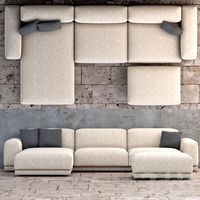
Vitra Place Sofa
...3ddd
vitra , place , модульный
vitra place sofa
turbosquid
$30
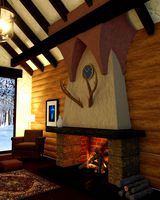
Chimney place
...quid
royalty free 3d model chimney place for download as obj on turbosquid: 3d models for games, architecture, videos. (1557502)
3ddd
$1
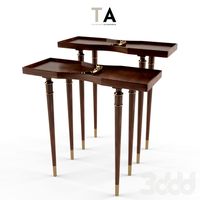
theodore alexander place to place
...pinched' rectangular tops with brass carrying handles to the centre, on turned and gilt highlighted legs with brass cappings.
turbosquid
$29

BOURKE PLACE
... free 3d model bourke place for download as 3ds, c4d, and skp on turbosquid: 3d models for games, architecture, videos. (1148874)
turbosquid
$10

Lounge Place
...free 3d model lounge place for download as ma, fbx, and blend on turbosquid: 3d models for games, architecture, videos. (1491379)
turbosquid
$7
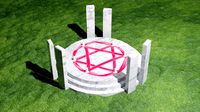
Place of Ritual
... 3d model place of ritual for download as blend, fbx, and obj on turbosquid: 3d models for games, architecture, videos. (1620181)
3d_export
$100
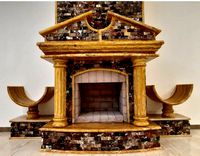
fair place
...ir place realistic stereoscopic natural size applied to communicate sed77665544@gmail.com what's up 00962788214043 i am ahmed