GrabCAD
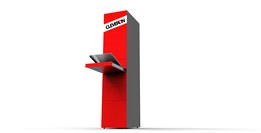
Cleveron Friction-Less Drawer
by GrabCAD
Last crawled date: 1 year, 11 months ago
Cleveron Friction-Less Drawer
Greetings GrabCAD community...
This is my first submission of "The Parcel Delivery System Challenge". Fortunately, I can still submit my ideas, since I know about the challenge only few days ago.
The basic idea to solve the major problem about the oversized package being jammed was to minimize the contact surface between the opened drawer and the drawer next above it. I use 5 small rod to accommodate that problem (as can be seen in the "cleveron #01.jpg" image). With this method, the friction can be minimized and localized in very small contact area. The friction will be localized in the surface of the rod.
For the drawer, I choose sheet metal material (stainless steel 316, 2mm thick). Compared to laminated hardboard, sheet metal is stronger so can minimize the thickness while maintain the strength. Thinner material we use, more room that we will get.
The sheet metal cover where the "friction rod" welded (spot weld-intermitten), will help to push the package if the package is a bit oversized. If the package oversized too much, and the pressure is much, it will prevent the drawer to close then the customer can choose bigger drawer. There is a spring that will open the cover automatically when the drawer pulled out. So, can operate the drawer with only one hand. There is also stopper in the back of the drawer. So, the drawer will stop slide outside the mainframe.
Here, I will try to explain how my proposed solution will solve the problems.
Problem-1
Allow the drawer to open at least 30mm, even if an oversized/expanding package is inserted.
Solution-1
The first solution can be check in the 3D model (and "cleveron #01.jpg"). I try to minimize the contact survace between the opened drawer and the drawer next upon it with 5 small diameter rods. When it closed, only the end of the rod will contacting the bottom surface of the drawer next above it. This way, the friction can be minimized and localized in very small area. The result, it will be easy to slide out.
To open the drawer at least 30mm automatically, I use "pull push" electromagnetic locking mechanism. It is commonly used in the RFID locking system, and widely available in the market, such as here (http://www.alibaba.com/product-detail/60kg-120Lbs-12vdc-or-24vdc-small_691592171.html). To open it at least 30mm, I choose 60kg electromagnetic lock. It used small amount of electricity (12V/100mA or 24V/50mA). It lock by pull the magnet with the electromagnet, and push by reverse the electromagnet polarity.
Problem-2
Maximize the size of package that can be inserted without jamming the drawer.
Solution-2
To solve this problem (to maximise the available room), I use sheet metal material. It is thin (2mm) but strong enough to hold the 5kg of package.
Problem-3
Guarantee the safety of the contents of the drawer(s).
Solution-3
I use 60kg electromagnetic locking system with push-pull feature. Its mean, to break the system need at least pull the drawer with 60kg of power. It is will be difficult since there is no handle in the drawer, and 60kg is quite heavy.
The connector of the locking system widely available in many kind of connector, including Molex Micro Fit 3.0 series connector (can be ordered in custom/preferred connector also).
Link for the electromagnetic locking system : http://www.alibaba.com/product-detail/60kg-120Lbs-12vdc-or-24vdc-small_691592171.html
Problem-4
Minimize the cost of the drawer solution in quantities of 1/100/1000 pcs.
Solution-4
For the drawer, mainly I use sheet metal. It is very easy to manufacture (cuting and bending process). And I am sure all sheet metal manufacturer will be able to handle that. I use 2mm thickness stainless steel 316. It is strong enough to hold the specified load and will be able to survive more than 8-10 years (2-3 times daily use). Its also less maintenance needed. For the framing, it is flexible. I use the stock framing (laminated hardboard). The framing can be using sheet metal and or steel/aluminum extrusion also.
I also develop custom drawer slide, which is stronger and less noisy compared to the slider that widely available in the market.
Problem-5
Allow easy and fast production and assembly.
Solution-5
The production was easy. I already modeling the drawer in sheet metal designing manner. Can generate flat pattern from the CAD model for cutting and bending purpose. The assembly was very easy as well. The stopper is different part and bolted to the drawer, so no need to access the drawer from the back if there is any problem appear.
Problem-6
Make use of widespread materials.
Solution-6
Mainly I use off the shelf part when designing the system. Fasteners, bearing, locking system, and etc.So all is "of the shelf part" except the sheet metal part, spring and the slider (the slider need CNC machining out of hardwood or aluminum).
Problem-7
Prevent the drawer from damaging itself in the case of misuse.
Solution-7
The choosen material was stainless steel, which is non-corrosive material. The bearing used also stainless steel bearing. So, it will be very durable.
Problem-8
Have a drawer load bearing capacity of at least 5kg (∽11 lb).
Solution-8
To accommodate the load, I designing the drawer with stainless steel sheet metal, so that it can hold the load. I also designing the custom slider that much more stronger and less noisy compared to the slider that commonly available in the market. However, I kept the design as simple as possible.
Thank you,
Arfi'an
Greetings GrabCAD community...
This is my first submission of "The Parcel Delivery System Challenge". Fortunately, I can still submit my ideas, since I know about the challenge only few days ago.
The basic idea to solve the major problem about the oversized package being jammed was to minimize the contact surface between the opened drawer and the drawer next above it. I use 5 small rod to accommodate that problem (as can be seen in the "cleveron #01.jpg" image). With this method, the friction can be minimized and localized in very small contact area. The friction will be localized in the surface of the rod.
For the drawer, I choose sheet metal material (stainless steel 316, 2mm thick). Compared to laminated hardboard, sheet metal is stronger so can minimize the thickness while maintain the strength. Thinner material we use, more room that we will get.
The sheet metal cover where the "friction rod" welded (spot weld-intermitten), will help to push the package if the package is a bit oversized. If the package oversized too much, and the pressure is much, it will prevent the drawer to close then the customer can choose bigger drawer. There is a spring that will open the cover automatically when the drawer pulled out. So, can operate the drawer with only one hand. There is also stopper in the back of the drawer. So, the drawer will stop slide outside the mainframe.
Here, I will try to explain how my proposed solution will solve the problems.
Problem-1
Allow the drawer to open at least 30mm, even if an oversized/expanding package is inserted.
Solution-1
The first solution can be check in the 3D model (and "cleveron #01.jpg"). I try to minimize the contact survace between the opened drawer and the drawer next upon it with 5 small diameter rods. When it closed, only the end of the rod will contacting the bottom surface of the drawer next above it. This way, the friction can be minimized and localized in very small area. The result, it will be easy to slide out.
To open the drawer at least 30mm automatically, I use "pull push" electromagnetic locking mechanism. It is commonly used in the RFID locking system, and widely available in the market, such as here (http://www.alibaba.com/product-detail/60kg-120Lbs-12vdc-or-24vdc-small_691592171.html). To open it at least 30mm, I choose 60kg electromagnetic lock. It used small amount of electricity (12V/100mA or 24V/50mA). It lock by pull the magnet with the electromagnet, and push by reverse the electromagnet polarity.
Problem-2
Maximize the size of package that can be inserted without jamming the drawer.
Solution-2
To solve this problem (to maximise the available room), I use sheet metal material. It is thin (2mm) but strong enough to hold the 5kg of package.
Problem-3
Guarantee the safety of the contents of the drawer(s).
Solution-3
I use 60kg electromagnetic locking system with push-pull feature. Its mean, to break the system need at least pull the drawer with 60kg of power. It is will be difficult since there is no handle in the drawer, and 60kg is quite heavy.
The connector of the locking system widely available in many kind of connector, including Molex Micro Fit 3.0 series connector (can be ordered in custom/preferred connector also).
Link for the electromagnetic locking system : http://www.alibaba.com/product-detail/60kg-120Lbs-12vdc-or-24vdc-small_691592171.html
Problem-4
Minimize the cost of the drawer solution in quantities of 1/100/1000 pcs.
Solution-4
For the drawer, mainly I use sheet metal. It is very easy to manufacture (cuting and bending process). And I am sure all sheet metal manufacturer will be able to handle that. I use 2mm thickness stainless steel 316. It is strong enough to hold the specified load and will be able to survive more than 8-10 years (2-3 times daily use). Its also less maintenance needed. For the framing, it is flexible. I use the stock framing (laminated hardboard). The framing can be using sheet metal and or steel/aluminum extrusion also.
I also develop custom drawer slide, which is stronger and less noisy compared to the slider that widely available in the market.
Problem-5
Allow easy and fast production and assembly.
Solution-5
The production was easy. I already modeling the drawer in sheet metal designing manner. Can generate flat pattern from the CAD model for cutting and bending purpose. The assembly was very easy as well. The stopper is different part and bolted to the drawer, so no need to access the drawer from the back if there is any problem appear.
Problem-6
Make use of widespread materials.
Solution-6
Mainly I use off the shelf part when designing the system. Fasteners, bearing, locking system, and etc.So all is "of the shelf part" except the sheet metal part, spring and the slider (the slider need CNC machining out of hardwood or aluminum).
Problem-7
Prevent the drawer from damaging itself in the case of misuse.
Solution-7
The choosen material was stainless steel, which is non-corrosive material. The bearing used also stainless steel bearing. So, it will be very durable.
Problem-8
Have a drawer load bearing capacity of at least 5kg (∽11 lb).
Solution-8
To accommodate the load, I designing the drawer with stainless steel sheet metal, so that it can hold the load. I also designing the custom slider that much more stronger and less noisy compared to the slider that commonly available in the market. However, I kept the design as simple as possible.
Thank you,
Arfi'an
Similar models
grabcad
free

SGCHL CLEVERON Parcel Delivery System
...electronic-locker-systems-with-ce-approved-ma1215l-.html)
3. sheet steel, bolts and nuts
the animation is loaded in mp4 format.
grabcad
free

Anti-stuck and lock solution
... the magnet is removed.
the springs eject drawer front and it opens.
simple and reliable system with no moving locking elements.
grabcad
free

Sheet metal stairs
...sheet metal stairs
grabcad
modular system,notice minimal welding,stainless steel
grabcad
free

The independent drawer solution
...nprcmorkc/cabinet-locks-catalog-1.html
anti stuck drawer cover made of transparent plastic to alow user see clearly the parcels.
grabcad
free

Analysis of Cleveron Drawer Problem
...analysis of cleveron drawer problem
grabcad
proposed solutions to improve existing drawer performance.
grabcad
free

Cleveron's parcel terminal drawer concept
...cleveron's parcel terminal drawer concept grabcad drawer operates similary to current as far as there is no oversized/expanded...
grabcad
free

cleveron oversize-able
...o make sure the slot safe / won't contaminate its slot-neighbor
the detail mechanism and description please see our pictures
grabcad
free

Parcel Delivery System solution
...wer.
on every drawer there is a sloping sheet metal plate that facilitate removing parcels and make the drawers independent.
grabcad
free

Cleveron drawer
...m stuck, i used 2 shaft between which stretched belt. support bracket mounted on shafts which does not excessively deformed belt.
thingiverse
free

Lock rings for smooth rods on printer by Peter_I
... them on the x-axis.
they could be used on y and z too, but i use other solutions there.
it is easy to use and quick to adjust.
Cleveron
grabcad
free

cleveron 2
...cleveron 2
grabcad
cleveron 2
grabcad
free

cleveron 1
...cleveron 1
grabcad
cleveron 1
grabcad
free

Cleveron drawer
...m stuck, i used 2 shaft between which stretched belt. support bracket mounted on shafts which does not excessively deformed belt.
grabcad
free

Analysis of Cleveron Drawer Problem
...analysis of cleveron drawer problem
grabcad
proposed solutions to improve existing drawer performance.
grabcad
free

Cleveron Parcel Delivery System
...
please see the included pdf for a complete writeup of my design and detailed explanations of every aspect of my decision making.
grabcad
free

Cleveron Parcel Delivery System Challenge
...me that will slightly compress as well as roll on the parcel.
youtube - https://www.youtube.com/channel/uczfrwbls5z_hmyop_jipkng
grabcad
free

Cleveron Parcel Delivery System Challenge
...lock opens the magnets comes into play pushes the the drawer.
youtube - https://www.youtube.com/channel/uczfrwbls5z_hmyop_jipkng
grabcad
free

Cleveron Smart-Go Parcel
...represented in this model. the cases also have features modeled for job-site assembly ease; hey why not :)
thanks for looking!!
grabcad
free

Cleveron System
...e of a time constrain i cannot finish everything for my proposal, hope the model and renderings will explain what i’m suggesting.
grabcad
free

Cleveron parcel delivery drawer opening alternative
...ening appears on front plate and performs as a handle if drawer is stuck. otherwise only a thin contour of an opening is visible.
Friction
3d_export
$14
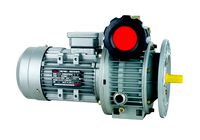
mb series planetary friction stepless transmission mbw-y 10 specifications in total
... mbw-y 10 specifications in total
3dexport
mb series planetary friction stepless transmission mbw-y (10 specifications in total)
3d_export
$5
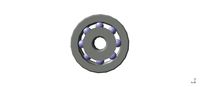
bearing
...relative motion to only the desired motion, and reduce friction between moving...
3d_export
$5

Ball Bearing
...functions while it facilitates motion: it carries loads, reduces friction and positions moving machine parts. ball bearings use balls...
3d_export
$10
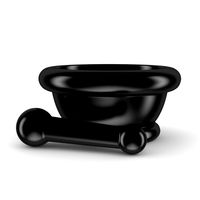
Kitchen Mortar 3D Model
...kitchen mortar 3d model 3dexport mortar black brushed friction room interior home house 3ds max cinema c4d mental...
3d_export
$10
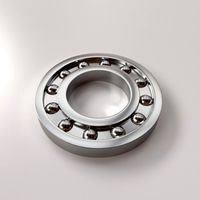
Ball Bearing 3D Model
...ball bearing 3d model 3dexport bearing machine element mechanical friction motion moving parts rotation axis bear ball ring spherical...
3d_export
$8
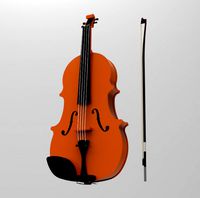
violin and bow
...hair (usually horse-tail hair) coated in rosin (to facilitate friction affixed to it. the vast majority of bows are...
3d_export
$7
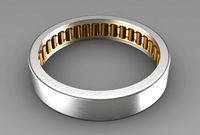
needle roller ball bearing
...small cylindrical rollers. these rollers are used to reduce friction of a rotating surface. needle roller bearings have a...
3d_export
$5

Disc Brake
...pads against a disc or a "rotor" to create friction this action slows the rotation of a shaft, such...
3d_export
$20

MSR500 Buried Scraper Conveyor
...of these forces is enough to overcome the external frictionl resistance and the weight of the material itself when...
3d_export
$16
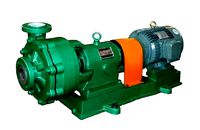
uhb-zk40 200 mortar pump 16 specifications in total
...suitable for use in the food industry. 6) low friction coefficient: the internal friction system of the pump is...
Less
design_connected
free

Less
...less
designconnected
molteni & c less free models computer generated 3d model. designed by jean nouvel.
3d_export
$10

Two Less tables 3D Model
...two less tables 3d model
3dexport
less molteni molteni&c table desk model
two less tables 3d model boroda 56653 3dexport
3d_export
$7
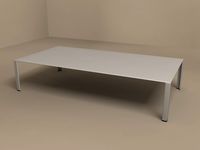
MolteniC table Less 3D Model
...c table less 3d model
3dexport
table desk molteni molteni&c less model
moltenic table less 3d model boroda 56651 3dexport
3d_export
$7

MolteniC table Less 3D Model
...c table less 3d model
3dexport
table desk molteni molteni&c less model
moltenic table less 3d model boroda 56650 3dexport
turbosquid
$19

Cisal Less New set
...3d model cisal less new set for download as max, obj, and fbx on turbosquid: 3d models for games, architecture, videos. (1470676)
turbosquid
$19

European Modern Couch - Less
...an modern couch - less for download as max, obj, fbx, and dwg on turbosquid: 3d models for games, architecture, videos. (1281460)
turbosquid
$4

Broom plastic less poly
... available on turbo squid, the world's leading provider of digital 3d models for visualization, films, television, and games.
design_connected
$13
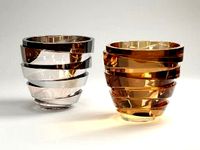
ANNA TORFS Parts Low Less Sculpture Vases
...anna torfs parts low less sculpture vases
designconnected
anna torfs parts low less sculpture vases computer generated 3d model.
turbosquid
$15
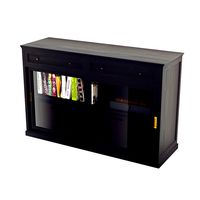
Ikea set MALSJO LESS chest of drawers
...alsjo less chest of drawers for download as max, obj, and fbx on turbosquid: 3d models for games, architecture, videos. (1607005)
turbosquid
$450
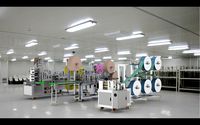
Ear less semi-automatic N95 mask machine Assembly
... semi-automatic n95 mask machine assembly for download as max on turbosquid: 3d models for games, architecture, videos. (1559662)
Drawer
3d_export
$5

chest of drawers with drawers sonata
...chest of drawers with drawers sonata
3dexport
chest of drawers with drawers sonata
archibase_planet
free
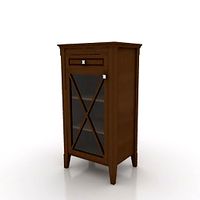
Drawer
...drawer
archibase planet
drawer case locker
drawer - 3d model for interior 3d visualization.
archibase_planet
free
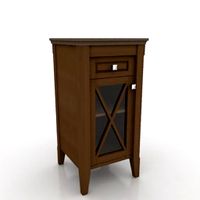
Drawer
...drawer
archibase planet
drawer dathroom furniture
drawer 896410 - 3d model for interior 3d visualization.
archibase_planet
free
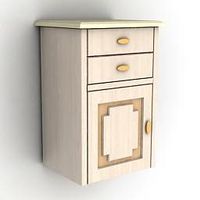
Drawer
...drawer
archibase planet
drawer shelving case
drawer - 3d model (*.3ds) for interior 3d visualization.
archibase_planet
free
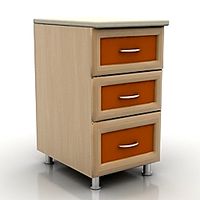
Drawer
...drawer
archibase planet
locker bureau drawer
drawer - 3d model (*.gsm+*.3ds) for interior 3d visualization.
archibase_planet
free

Drawer
...drawer
archibase planet
case drawer locker
drawer - 3d model (*.gsm+*.3ds) for interior 3d visualization.
archibase_planet
free
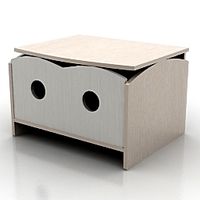
Drawer
...drawer
archibase planet
locker drawer case
drawer - 3d model (*.gsm+*.3ds) for interior 3d visualization.
archibase_planet
free

Drawer
...drawer
archibase planet
drawer case bathroom furniture
drawer 896411 - 3d model for interior 3d visualization.
archibase_planet
free
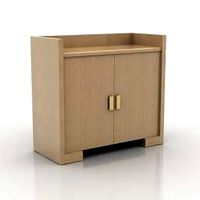
Drawer
...drawer
archibase planet
locker drawer case
drawer - 3d model (*.gsm+*.3ds) for interior 3d visualization.
archibase_planet
free
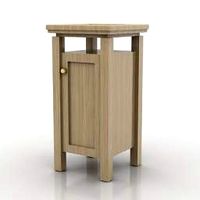
Drawer
...drawer
archibase planet
locker case drawer
drawer - 3d model (*.gsm+*.3ds) for interior 3d visualization.