Thingiverse
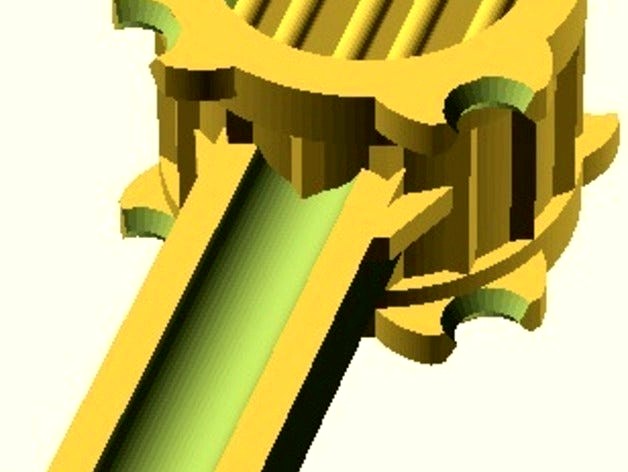
Centi PET Re-Extruder: Heating-Chamber by mechadense
by Thingiverse
Last crawled date: 3 years ago
The goal is to make 3mm filament from PET drinking Bottles.
NOTE: This needs serious redesign!
(To this melting chamber any kind of drive can be mounted and any kind of plastic can bee fed but a PET-band stepper-feed is planned edit: is considered)
The he Centi PET Re-Extruder shall be easier to build and cheaper than exiting re-extruder projects. This shall be reached by making it smaller (20cm desktop size instead of 1m workbench size) and requiring its maximum output speed not to be very high (>= one printer input speed).
For a fully functional system additionally to this melting chamber there will be needed:
PET Cutter (A); PET Band Feeder & Guider (B); Filament cooler & catcher (C)
Those are not yet constructed.
This Melting chamber is Heavily influenced by the existing projects:
http://reprap.org/wiki/Web4Deb_extruder
http://www.appropedia.org/Waste_plastic_extruder
http://www.thingiverse.com/thing:12948
http://recyclebot.tumblr.com/
http://www.kickstarter.com/projects/rocknail/filabot-plastic-filament-maker
The only differences are that it is smaller (thumb sized melting chamber) and it has some additional features which are only possible since it's a 3d printed design. Those features will be more thorougly discussed in the following design decisions section:
DESIGN DECISIONS:
Since its smaller size it has much more surface area per volume and thus huge-er thermal losses. So a bit more care must be taken for thermal isolation.
SEE: [INSTRUCTIONS -> Assembly] for application of thermal isolation.
The chamber is open on both ends => easy cleaning easy nozzlechange and nice thermal isolation with fibreglas-PCB endplates.
The chamber is symmetrical => no wrong assembly possible.
Lots of spikes (16) and wedgecuts (2) provide air pockets under the isolation to give additional thermal isolation.
The screw aligners are open and sharp pointed for minimized thermal contact to the screws.
Wall thicknesses are kept minimal for lower material volume and thus price.
Lamellas:
PET has a very high thermal resistance [0.28W / (m*K)].
The steel lamellas [shapeways infused steel: 22.6 W/(m*K)] decrease the termal equilibration time quite a lot.
The gap between lamellas should be choosen as a tradeof. With smaller gap size the maximum feed speed for reasonable thermal exchange rises but if the gaps become too narrow viscous friction will kick in (laminar flow). An optimal geometry would require numerical simulations and narrowing gaps (this is overkill).
The minimum lamella thickness is given by the printing process and should be around 1.5mm for steel prints.
The outer isolation (thermal resistance similar to PET) should be thicker than the distance between lamellas. I hope the airpockets are ganna help here. As of now I've choosen the gap size as small as possible so that it remains reasonably cleanable but it wouldn't hurt to do some conservative estimative calculations. (TODO)
I chose PET as primary feeding material out of following reasons:
1) Drinking Bottle PET has a reasonable low melting point ( 230°C ) (due to some additives ?) SEE:
http://blog.reprap.org/2009/03/drink-bottle-feedstock.html
I tested melting it with my soldering iron set to 220°C and it melted easily!
2) It can be cut to very slim long stripes which lend themselve for feeding into a small melting chamber entrance with an hobbed bolt drive (no auger drill drive intended)
For cutting devices I found this nice website:
http://www.utsumi.com.br/pet/English/filetador/index.html
The first two steps in PET bottle processing must be treated with different parts that are yet to be constructed
Centi PET Cutter -- see (A) below
Centi PET Band Feeder & Guider -- see (B) below
3) Very good mechanical properties prints similar to PLA (diff temp) but is not brittle at all.
Though hygroscopicness & re-crystallisation may degrade it a bit.
4) IMO it smells less obnoxious than HDPE fumes
################################### TODO
(A) Petcutter
Is it possible to construct a small one that is easy to handle?
(B) Feeder & Guider
the drive mechanism must solve
backlog
PET band creasing avoidance or control over it ("snakelooping")
"channel to be the thickness of the folded strip"
=> maybe too thinn to print.
directly feeding the pet band to a printer?
=> probably not for an bowden tube printer.
(C) Filament Cooler & Catcher
important for constant diameter
design so that it can be directly fed into a bowden tube
####################################
NOTE: This needs serious redesign!
(To this melting chamber any kind of drive can be mounted and any kind of plastic can bee fed but a PET-band stepper-feed is planned edit: is considered)
The he Centi PET Re-Extruder shall be easier to build and cheaper than exiting re-extruder projects. This shall be reached by making it smaller (20cm desktop size instead of 1m workbench size) and requiring its maximum output speed not to be very high (>= one printer input speed).
For a fully functional system additionally to this melting chamber there will be needed:
PET Cutter (A); PET Band Feeder & Guider (B); Filament cooler & catcher (C)
Those are not yet constructed.
This Melting chamber is Heavily influenced by the existing projects:
http://reprap.org/wiki/Web4Deb_extruder
http://www.appropedia.org/Waste_plastic_extruder
http://www.thingiverse.com/thing:12948
http://recyclebot.tumblr.com/
http://www.kickstarter.com/projects/rocknail/filabot-plastic-filament-maker
The only differences are that it is smaller (thumb sized melting chamber) and it has some additional features which are only possible since it's a 3d printed design. Those features will be more thorougly discussed in the following design decisions section:
DESIGN DECISIONS:
Since its smaller size it has much more surface area per volume and thus huge-er thermal losses. So a bit more care must be taken for thermal isolation.
SEE: [INSTRUCTIONS -> Assembly] for application of thermal isolation.
The chamber is open on both ends => easy cleaning easy nozzlechange and nice thermal isolation with fibreglas-PCB endplates.
The chamber is symmetrical => no wrong assembly possible.
Lots of spikes (16) and wedgecuts (2) provide air pockets under the isolation to give additional thermal isolation.
The screw aligners are open and sharp pointed for minimized thermal contact to the screws.
Wall thicknesses are kept minimal for lower material volume and thus price.
Lamellas:
PET has a very high thermal resistance [0.28W / (m*K)].
The steel lamellas [shapeways infused steel: 22.6 W/(m*K)] decrease the termal equilibration time quite a lot.
The gap between lamellas should be choosen as a tradeof. With smaller gap size the maximum feed speed for reasonable thermal exchange rises but if the gaps become too narrow viscous friction will kick in (laminar flow). An optimal geometry would require numerical simulations and narrowing gaps (this is overkill).
The minimum lamella thickness is given by the printing process and should be around 1.5mm for steel prints.
The outer isolation (thermal resistance similar to PET) should be thicker than the distance between lamellas. I hope the airpockets are ganna help here. As of now I've choosen the gap size as small as possible so that it remains reasonably cleanable but it wouldn't hurt to do some conservative estimative calculations. (TODO)
I chose PET as primary feeding material out of following reasons:
1) Drinking Bottle PET has a reasonable low melting point ( 230°C ) (due to some additives ?) SEE:
http://blog.reprap.org/2009/03/drink-bottle-feedstock.html
I tested melting it with my soldering iron set to 220°C and it melted easily!
2) It can be cut to very slim long stripes which lend themselve for feeding into a small melting chamber entrance with an hobbed bolt drive (no auger drill drive intended)
For cutting devices I found this nice website:
http://www.utsumi.com.br/pet/English/filetador/index.html
The first two steps in PET bottle processing must be treated with different parts that are yet to be constructed
Centi PET Cutter -- see (A) below
Centi PET Band Feeder & Guider -- see (B) below
3) Very good mechanical properties prints similar to PLA (diff temp) but is not brittle at all.
Though hygroscopicness & re-crystallisation may degrade it a bit.
4) IMO it smells less obnoxious than HDPE fumes
################################### TODO
(A) Petcutter
Is it possible to construct a small one that is easy to handle?
(B) Feeder & Guider
the drive mechanism must solve
backlog
PET band creasing avoidance or control over it ("snakelooping")
"channel to be the thickness of the folded strip"
=> maybe too thinn to print.
directly feeding the pet band to a printer?
=> probably not for an bowden tube printer.
(C) Filament Cooler & Catcher
important for constant diameter
design so that it can be directly fed into a bowden tube
####################################
Similar models
thingiverse
free
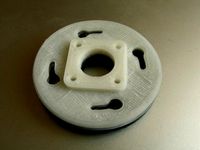
Centi PET Re-Extruder: Expander Flange by mechadense
...pcb isolation plates which lead to the heating chamber. on the flat side (cold side) any conceivable input device can be mounted.
grabcad
free

Filament Feeder
...e to interference with internal components. worked out fine and combined it with the filament spool holder i've also posted.
thingiverse
free
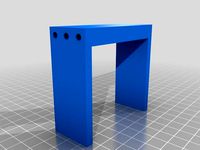
Filament Feeder/Guider by joeyimprota
...filament feeder/guider by joeyimprota
thingiverse
a three hole filament feeder primarily for the flash forge finder
thingiverse
free

Bird cage feeder
...bird cage feeder
thingiverse
bird cage feed holder. printer at 0.3 with pet filament.
thingiverse
free
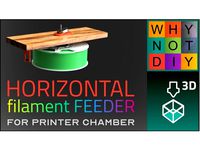
Horizontal Filament Feeder for Printer Chamber by theveel_com
...thingiverse
https://youtu.be/qe8cbwm1nek
more about designhttps://theveel.com/3d/horizontal-filament-feeder-for-printer-chamber/
thingiverse
free

PET Bottle Bird Feeder (Pet Flaschen Vogel Futter) by campilot
...schen vogel futter) by campilot
thingiverse
two different pet bottle birds feeder (small & big platform)
mounting ring (tpu)
thingiverse
free

Simple water feeder - PET bottle by Sedivec
...simple water feeder - pet bottle by sedivec
thingiverse
watter feeder for pets and birds, for a pet bottle
thingiverse
free
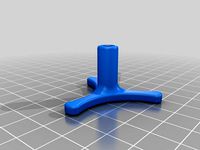
Stepper motor feed knob by cfeniak
... designed for use with direct drive filament setups for manually feeding filament. push fit. smaller sized knob is big enough.
thingiverse
free

Bird feeder on PET bottle by jirkabr
...the frequency of bird visits fully matched the larger type, with losses by dropping feed on the ground being significantly lower.
3dwarehouse
free

Dog Feeder
...me. sized for large 100 lb dog, but the 'bowl' can be sized as needed for smaller dogs. #pets #dogs #woodworking #storage
Centi
thingiverse
free
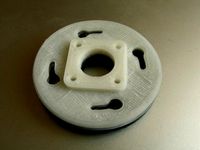
Centi PET Re-Extruder: Expander Flange by mechadense
...pcb isolation plates which lead to the heating chamber. on the flat side (cold side) any conceivable input device can be mounted.
cg_trader
free

Centi
...centi
cg trader
centi 3d, available in ztl, artificial artificial challenge character creature, ready for 3d animation and ot
3dwarehouse
free
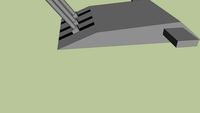
46 cm gun
...gun battery found on the ijn yamato #46 #battleship #centi #cm #gun #meter...
3dwarehouse
free
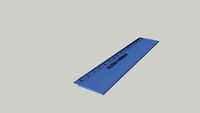
Shatter-resistant ruler
...no branding and marked in millimeters and centimeters #centi #centietres #cm #measure #milli #millimetres #mm #rule #ruler...
3dwarehouse
free

Centipede arcade game Rev.1
... now 100% accurate. thanks to zork40 for all the buttons. #arcades #atari #centi #coinop #game #millipede #pede #trackball #video
3dwarehouse
free
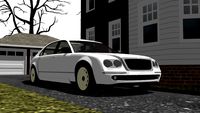
Enus Cognoscenti Landaulet (GTA IV)
...landaulet #large #limousine #luxury #maisak #maybach #maybach62 #mercedesbenz #rollsroyce #sedan #sttugart #theft #tokyo #xrw960h
Mechadense
thingiverse
free
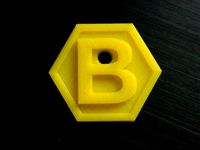
Bee ... by mechadense
...bee ... by mechadense
thingiverse
print request at
linuxwochen 2015 vienna austriahttp://www.linuxwochen.at/wien/
thingiverse
free
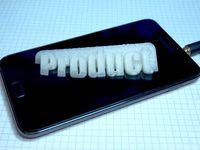
Product by mechadense
...product by mechadense
thingiverse
just a prop. convert your phone to a fake atomically precise personal fabricator.
thingiverse
free
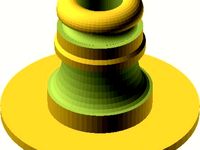
Water Hose Connector by mechadense
...water hose connector by mechadense
thingiverse
compatible with the gardener(tm) system.
thingiverse
free
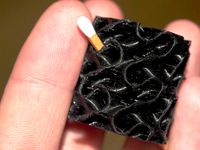
Gyroid Cylinder by mechadense
...iverse
made with minisagecadashttp://www.thingiverse.com/thing:40210
command: intersection2(cylinderc(30,60),gyroid_left(3,25))
thingiverse
free

Sheet Pin by mechadense
...nse
thingiverse
a pin & clamping ring combo to clamp thin plates together.
e.g. usable as connectors for scissor mechanisms.
thingiverse
free
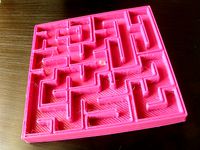
Maze 10x10 - simple by mechadense
...maze 10x10 - simple by mechadense
thingiverse
singly connected. every pair of points can be used as start and goal.
thingiverse
free
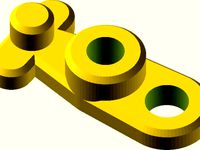
Nail-to-Tentpeg Converter by mechadense
...nail-to-tentpeg converter by mechadense
thingiverse
make tentpegs from nails with this little heads.
customize to your needs.
thingiverse
free
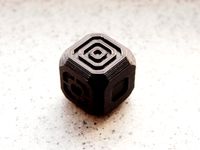
Simplistic Symmetric Die by mechadense
...simplistic symmetric die by mechadense
thingiverse
for gaming afk.
you can support me by ordering there:shapeways entry
thingiverse
free
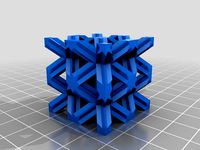
111 spaceframe demo by mechadense
...111 spaceframe demo by mechadense
thingiverse
if you want to know how a 111 space-frame looks like here it is.
thingiverse
free
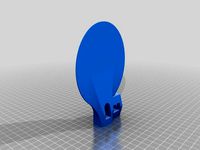
Toy Propeller Fin by mechadense
...toy propeller fin by mechadense
thingiverse
fin for my old two blade propeller thing:http://www.thingiverse.com/thing:8178
Chamber
turbosquid
$15
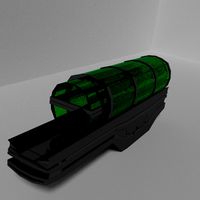
Chamber
...rbosquid
royalty free 3d model chamber for download as blend on turbosquid: 3d models for games, architecture, videos. (1240986)
3d_export
$6
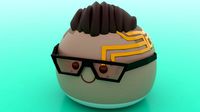
Chamber
...chamber
3dexport
squish dumpling avatars of the valorant agents.
turbosquid
$53
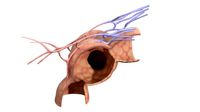
Alveolus Chamber
... available on turbo squid, the world's leading provider of digital 3d models for visualization, films, television, and games.
turbosquid
free

Underground chamber
... available on turbo squid, the world's leading provider of digital 3d models for visualization, films, television, and games.
turbosquid
free
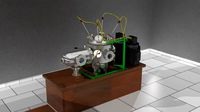
Vacuum chamber
... available on turbo squid, the world's leading provider of digital 3d models for visualization, films, television, and games.
turbosquid
$10

disinfection chamber
...on chamber for download as blend, 3ds, dae, fbx, obj, and stl on turbosquid: 3d models for games, architecture, videos. (1671962)
3d_export
$25
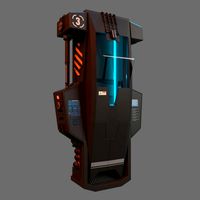
Hypersleep Chamber
..., the users are usually clad in either sleepwear or underwear to prevent clothes and/or armor to become frozen to the users body.
turbosquid
$2

Xenomorph Incubation Chamber
...y free 3d model xenomorph incubation chamber for download as on turbosquid: 3d models for games, architecture, videos. (1705895)
3d_export
$7

chambers bar stools
...chambers bar stools
3dexport
name:
turbosquid
$59

Chamber Pendant Light
...yalty free 3d model chamber pendant light for download as max on turbosquid: 3d models for games, architecture, videos. (1291559)
Pet
3d_export
$5
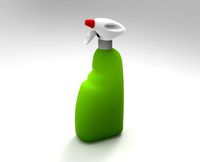
PET Bottle
...pet bottle
3dexport
this is a pet bottle of clorina, deagreaser, glass cleaner of something similar
turbosquid
$35
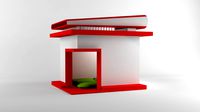
Caxinha Pet
...osquid
royalty free 3d model caxinha pet for download as skp on turbosquid: 3d models for games, architecture, videos. (1178810)
turbosquid
$14
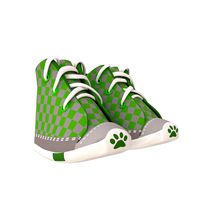
Pet Shoes
...rbosquid
royalty free 3d model pet shoes for download as max on turbosquid: 3d models for games, architecture, videos. (1332619)
turbosquid
$8
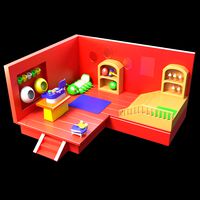
Pet Shop In
...bosquid
royalty free 3d model pet shop in for download as ma on turbosquid: 3d models for games, architecture, videos. (1388224)
turbosquid
$5

Pet Bowl
...urbosquid
royalty free 3d model pet bowl for download as max on turbosquid: 3d models for games, architecture, videos. (1709411)
turbosquid
$1

Bed Pet
...turbosquid
royalty free 3d model bed pet for download as ige on turbosquid: 3d models for games, architecture, videos. (1537522)
3d_export
$10

Wood Pet House Pet
...~ 100,000 model parts: 1 texture format: .png .jpg resolution: 1024*1024 pbr in substance painter formats: .obj .gltf .fbx .blend
3d_export
$5

pet house 001
...pet house 001
3dexport
house for pets: cat or small dog breeds.
turbosquid
$18
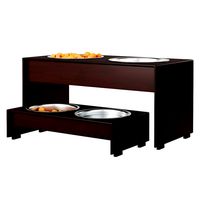
Pet feeder
...ee 3d model pet feeder for download as max, max, fbx, and obj on turbosquid: 3d models for games, architecture, videos. (1559898)
3d_ocean
$4
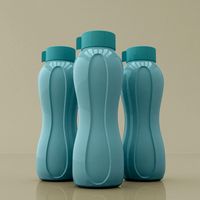
Pet Bottle
...max 2013. rendering, material and lighting varay. the polygon counting 450797. no extra material used. it is a house hold things.
Heating
3d_export
$5

heat
...heat
3dexport
heat tool
3ddd
$1
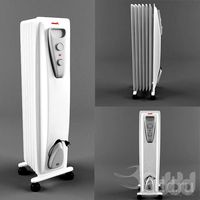
electric heating
...electric heating
3ddd
обогреватель
electric heating
3d_export
$6
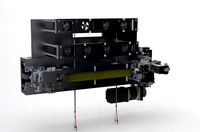
The heating module
...any questions also you can email to me. designed with solidworks 2017, render with keyshot **************************************
turbosquid
free
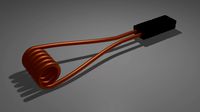
Heating Rod
...rod
turbosquid
free 3d model heating rod for download as obj on turbosquid: 3d models for games, architecture, videos. (1482690)
turbosquid
$2
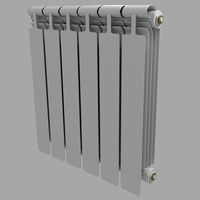
Heating Radiator
...
royalty free 3d model heating radiator for download as blend on turbosquid: 3d models for games, architecture, videos. (1561908)
3d_export
$35
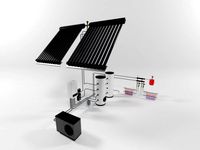
heating instalation with heat pump and solar system
...el , please contact me. before buying a model, you can try to download one of my free models and testing. thank you for watching.
turbosquid
$29
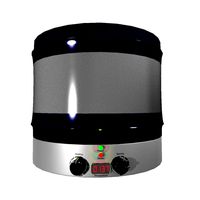
Heating Mantle
... available on turbo squid, the world's leading provider of digital 3d models for visualization, films, television, and games.
turbosquid
$25
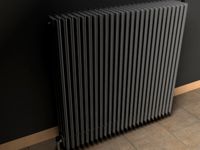
Heating Radiator
... available on turbo squid, the world's leading provider of digital 3d models for visualization, films, television, and games.
turbosquid
$20
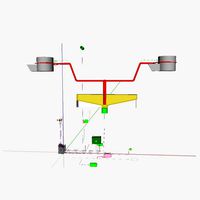
AT_airship_control_stand_(heated)
... available on turbo squid, the world's leading provider of digital 3d models for visualization, films, television, and games.
turbosquid
$20
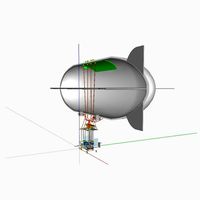
AT_airship_(heated)
... available on turbo squid, the world's leading provider of digital 3d models for visualization, films, television, and games.
Extruder
3ddd
$1
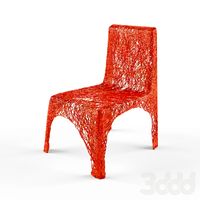
Extruded Chair
...extruded chair
3ddd
extruded , tom dixon
inspired by tom dixon extruded chair
turbosquid
$15
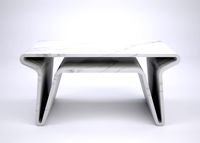
Extruded Table
... extruded table for download as blend, dae, fbx, obj, and stl on turbosquid: 3d models for games, architecture, videos. (1634137)
turbosquid
$2
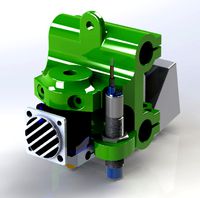
3D Printer Extruder
...d
royalty free 3d model 3d printer extruder for download as on turbosquid: 3d models for games, architecture, videos. (1537359)
turbosquid
$1
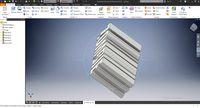
Zombie extruded text
...oyalty free 3d model zombie extruded text for download as obj on turbosquid: 3d models for games, architecture, videos. (1322198)
turbosquid
$4
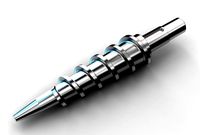
Extruder conical screw
...el extruder conical screw for download as sldpr, ige, and stl on turbosquid: 3d models for games, architecture, videos. (1524433)
turbosquid
$50
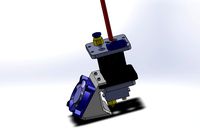
3d PRINTER - Extruder
... available on turbo squid, the world's leading provider of digital 3d models for visualization, films, television, and games.
turbosquid
$15
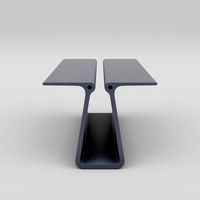
Extruded Table 2
...xtruded table 2 for download as blend, dae, fbx, obj, and stl on turbosquid: 3d models for games, architecture, videos. (1621846)
turbosquid
$10

Maya Extrude Tool
... available on turbo squid, the world's leading provider of digital 3d models for visualization, films, television, and games.
3d_export
$5
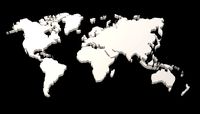
world earth extrude map
...world earth extrude map
3dexport
3ddd
$1

Simply Elegant Extruded Tree Coffee Table Design
...ble by link studios. the silhouette of a tree is visible at one angle, extruded from the surface to create the support structure.
Re
3ddd
$1
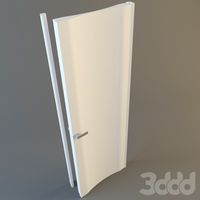
RES 10_8
...res 10_8
3ddd
res , дверь
производитель res модель 10.8
turbosquid
$7
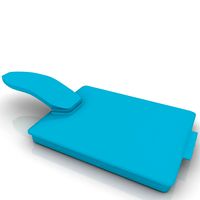
Re
... available on turbo squid, the world's leading provider of digital 3d models for visualization, films, television, and games.
design_connected
$18
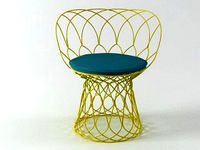
Re-trouvé
...re-trouvé
designconnected
emu group re-trouvé chairs computer generated 3d model. designed by patricia urquiola.
design_connected
$16

Re-turned
...
photo-realistic 3d models of the re-turned table accessories from beller for 3d architectural and interior design presentations.
3ddd
free
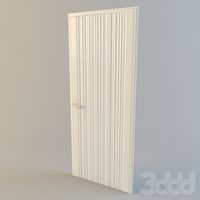
дверь RES WAVE
... дверь , карим рашид
производитель res италия модель wave
turbosquid
$1

Table Re
...ree 3d model table re for download as ma, obj, fbx, and blend on turbosquid: 3d models for games, architecture, videos. (1233574)
3ddd
$1

Do-lo-Res
... угловой
диван фабрика do-lo-res компонуется из отдельных боксов, разнообразных размеров и тканей.
design_connected
$16
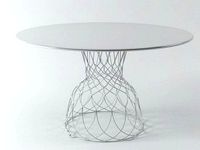
Re-trouvé Tables
...re-trouvé tables
designconnected
emu group re-trouvé tables computer generated 3d model. designed by urquiola, patricia.
design_connected
$11
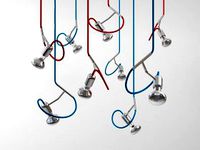
Re-flect pendant
...re-flect pendant
designconnected
steng licht re-flect pendant computer generated 3d model. designed by e27 berlin.
design_connected
$11
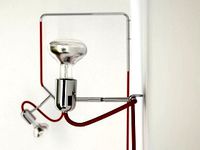
Re-flect wall
...re-flect wall
designconnected
steng licht re-flect wall computer generated 3d model. designed by e27 berlin.