Thingiverse
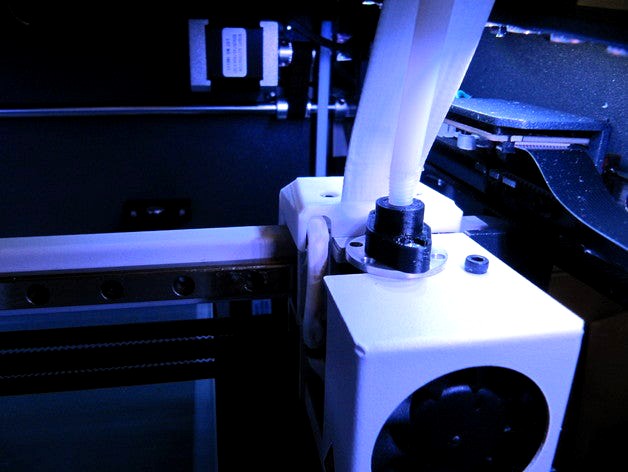
BCN3D Sigma bowden tube retention fitting by freddotu
by Thingiverse
Last crawled date: 3 years ago
8 July 2016 EDIT:
I've created an edit lower in this document with a metal shim that performs better, but may be challenging to construct without suitable tools. Due to that complication, I've also created a 3d printable shim here:http://www.thingiverse.com/thing:1664774
It also works better than this threaded version, but I've left the threaded version in place, perhaps to assist someone else with a similar need, but not precisely this application.
A remix of sorts, although not by much. I took the concept from StikDesign and "streamlined" it a bit, removing material and reducing the amount of support (and time) necessary to accomplish the same result. Credit goes to StikDesign for coming up with the threaded tube concept, an elegantly simple solution for a nuisance of sorts.
The BCN3D Sigma dual extruder printer is a work of technological art. The prints are beautiful, even at 300 micron layer height. I understand that a few machines suffer from bowden tube creep and release, as did mine.
This fitting, properly created, processed and installed, solves the tube creep.
Another EDIT!
I wasn't happy with the weakening of the bowden tube, nor with the need to recalibrate after each bowden tube removal. With a suggestion from MatterHackers, I came up with the added item to this post.
It's a conventional feeler gauge from the auto parts store. This one is 0.88 mm thick, which appears to be nearly perfect to apply gentle but firm lifting force to the underside of the gripper release ring.
I used a series of drills, ending with 8.5 mm. Unfortunately, the feeler gauge is made of seriously strong grade steel and I pretty much destroyed the cheap bits from, well, where does one buy cheap stuff today?
With help from an abrasive cutting wheel, I chopped open one end, tapered the "fingers" and cleaned up the burrs. Using the TLAR method, a mid-point cut and two ninety-degree bends, the result is superior to my printed fitting.
I've created an edit lower in this document with a metal shim that performs better, but may be challenging to construct without suitable tools. Due to that complication, I've also created a 3d printable shim here:http://www.thingiverse.com/thing:1664774
It also works better than this threaded version, but I've left the threaded version in place, perhaps to assist someone else with a similar need, but not precisely this application.
A remix of sorts, although not by much. I took the concept from StikDesign and "streamlined" it a bit, removing material and reducing the amount of support (and time) necessary to accomplish the same result. Credit goes to StikDesign for coming up with the threaded tube concept, an elegantly simple solution for a nuisance of sorts.
The BCN3D Sigma dual extruder printer is a work of technological art. The prints are beautiful, even at 300 micron layer height. I understand that a few machines suffer from bowden tube creep and release, as did mine.
This fitting, properly created, processed and installed, solves the tube creep.
Another EDIT!
I wasn't happy with the weakening of the bowden tube, nor with the need to recalibrate after each bowden tube removal. With a suggestion from MatterHackers, I came up with the added item to this post.
It's a conventional feeler gauge from the auto parts store. This one is 0.88 mm thick, which appears to be nearly perfect to apply gentle but firm lifting force to the underside of the gripper release ring.
I used a series of drills, ending with 8.5 mm. Unfortunately, the feeler gauge is made of seriously strong grade steel and I pretty much destroyed the cheap bits from, well, where does one buy cheap stuff today?
With help from an abrasive cutting wheel, I chopped open one end, tapered the "fingers" and cleaned up the burrs. Using the TLAR method, a mid-point cut and two ninety-degree bends, the result is superior to my printed fitting.
Similar models
cults
free

BCN3D Sigma (Anti-Popping) Bowden Tube Shim
...gma (anti-popping) bowden tube shim
cults
bcn3d sigma (anti-popping) bowden tube shim
bcn3d sigma (anti-popping) bowden tube shim
cults
free

BCN3D Sigma (Anti-Popping) Bowden Tube Locked Shim
...wden tube locked shim
cults
bcn3d sigma (anti-popping) bowden tube locked shim
bcn3d sigma (anti-popping) bowden tube locked shim
thingiverse
free

BCN3D Sigma Bowden Creep Fixer by kirberich
... extruder screws.
i've got a small redesign in mind that should make removal simpler, but for me it seems fine the way it is.
thingiverse
free

BCN3D Sigma bowden tube shim by freddotu
...tary tool.
now that i have a simple design, i felt there was no reason it should be a problem to build in pla, hence this thingy.
thingiverse
free
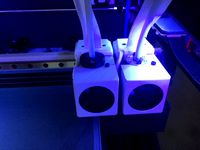
attachment bowden tube by StikDesign
..., and the tube with outer m6 thread (this is done manually!). ths way the tube does not get squeezed and won't pop out again.
thingiverse
free

BCN3D Sigma (Anti-Popping) Bowden Tube Shim by David_Mussaffi
...bcn3d sigma (anti-popping) bowden tube shim by david_mussaffi
thingiverse
https://youtu.be/pojbhlyrjl8
3d model moved to cults3d
thingiverse
free

BCN3D SIGMA Bowden Spacer by chrislm
...he axis, without need to paste it on the printer enclosure.
you could use the open one if you don't want to remove the bowden
cults
free
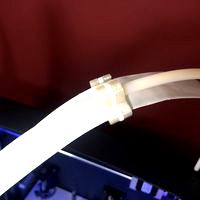
BCN3D Sigma Bowden Cable Clip (Dual Extrusion / 2 Color)
... 2 color)
cults
bcn3d sigma bowden cable clip (dual extrusion / 2 color)
bcn3d sigma bowden cable clip (dual extrusion / 2 color)
thingiverse
free

BCN3D Sigma Bowden Cable Clip (Dual Extrusion / 2 Color) by David_Mussaffi
...update to the default bowden cable clip that's included in the bcn3d sigma 3d printer.
original design by bcn3d technologies.
thingiverse
free
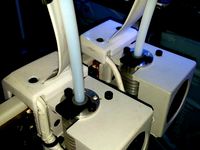
BCN3D SIGMA bowden clip by soliddo
...bcn3d sigma bowden clip by soliddo
thingiverse
bowden clip with the nozzle extruder diameter
Freddotu
thingiverse
free
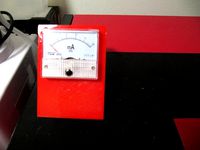
Ammeter mount box by freddotu
... do it here too. i'm not a programmer, so the openscad code is going to be sloppy, but not impossible to understand (i hope.)
thingiverse
free

BCN Sigma extended spool holder by freddotu
...at max heat setting.
one could probably get away with using pla to print these, but they may break sooner with pla than with abs.
thingiverse
free

BCN3D Sigma bowden tube shim by freddotu
...tary tool.
now that i have a simple design, i felt there was no reason it should be a problem to build in pla, hence this thingy.
thingiverse
free

Gandlaf The White's staff by freddotu
.... rafts or brims may be necessary to get a good bond on the build plate for the circles, however, as the wall thickness is small.
thingiverse
free
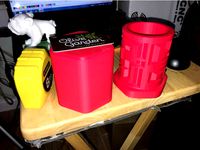
Labyrinth Gift Box Upscaled by freddotu
...dded a modified lid which has a 3 mm x 40 mm coin slot, allowing this to become an easily opened (relatively speaking) coin bank.
thingiverse
free

Light Bar Bracket for encapsulated LED strip on 2020 extrusion by freddotu
... other end serves as a convenient cap.
openscad creation files included, if you find you need to tweak a dimension here or there.
thingiverse
free

Flux Delta external filament spool holder by freddotu
... nor on the rendered model in openscad.
it's my first contribution to thingiverse and i hope others will make good use of it.
Bcn3D
thingiverse
free
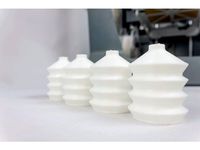
BCN3D Bellow by BCN3D
...ech
bcn3d google+: https://plus.google.com/u/2/106660239696256442101
about bcn3d technologies - https://www.bcn3dtechnologies.com
thingiverse
free
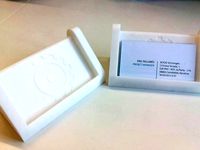
BCN3D Bussiness Card Holder by BCN3D
...ech
bcn3d google+: https://plus.google.com/u/2/106660239696256442101
about bcn3d technologies - https://www.bcn3dtechnologies.com
thingiverse
free

Vertical Bowden BCN3D by BCN3D
...ech
bcn3d google+: https://plus.google.com/u/2/106660239696256442101
about bcn3d technologies - https://www.bcn3dtechnologies.com
thingiverse
free
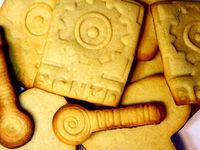
Cookie Cutter - BCN3D & COLORFILA LOGO by BCN3D
...ech
bcn3d google+: https://plus.google.com/u/2/106660239696256442101
about bcn3d technologies - https://www.bcn3dtechnologies.com
thingiverse
free
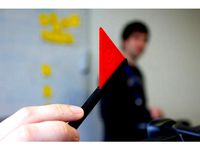
BCN3D Do Not Disturb Flag by BCN3D
...ech
bcn3d google+: https://plus.google.com/u/2/106660239696256442101
about bcn3d technologies - https://www.bcn3dtechnologies.com
thingiverse
free
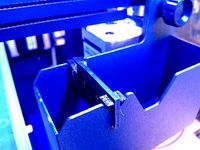
BCN3D Sigma Cloth Support by BCN3D
...ech
bcn3d google+: https://plus.google.com/u/2/106660239696256442101
about bcn3d technologies - https://www.bcn3dtechnologies.com
thingiverse
free
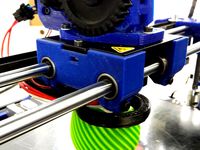
BCN3D+ STRONG CARRIAGES by fabiano79
...bcn3d+ strong carriages by fabiano79
thingiverse
this is an upgrade for the extruder carriages of the bcn3d+ printer.
thingiverse
free
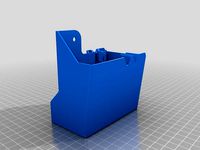
BCN3D Sigma - Jumbo Purge Bucket by BCN3D
...ech
bcn3d google+: https://plus.google.com/u/2/106660239696256442101
about bcn3d technologies - https://www.bcn3dtechnologies.com
thingiverse
free

Pen Holder by BCN3D
...ech
bcn3d google+: https://plus.google.com/u/2/106660239696256442101
about bcn3d technologies - https://www.bcn3dtechnologies.com
thingiverse
free

Hollow Draudi by BCN3D
...ech
bcn3d google+: https://plus.google.com/u/2/106660239696256442101
about bcn3d technologies - https://www.bcn3dtechnologies.com
Retention
thingiverse
free
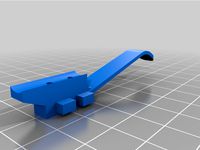
Arrow Retention Spring for Mainhunter Mamba by Isusovich
...arrow retention spring for mainhunter mamba by isusovich
thingiverse
arrow retention spring
thingiverse
free

SO239 cap with retention by duglia
...file for size.
added a groove for a grommet and a small pass trough for a retention cord.
as usual, your size and scale may vary.
3dfindit
free

Circular Connector Locking & Retention
...circular connector locking & retention
3dfind.it
catalog: te connectivity
thingiverse
free

Casement window screen retention clip by Vartech_Dynamics
...erse
this retention clip is for casement window screens. this allows the screen to be inserted snuggly into the window opening.
thingiverse
free

Cisco 7821 Phone Retention Tab by aguzinski
...on tab by aguzinski
thingiverse
replacement retention tab for the cisco 7821 phone. holds phone while base is mounted to a wall.
thingiverse
free

Mag Pouch Bungee Side Retention by qblackfoxp
...etention.
i would use petg or abs, but i'm sure pla could work but wouldn't hold up long for the high retention version.
thingiverse
free

Tesla Subwoofer to SoundQubed Retention Bracket by Naonak
...sn't really necessary, as the subwoofer is a pretty snug fit on its own, but you can always add this is some extra retention.
thingiverse
free

Powerpole Retention Clip for 1327 Housing
...5-45 amps), commonly used in frc. there are locking pins that slide into the holes formed by 2 or more joined powerpole housings.
thingiverse
free
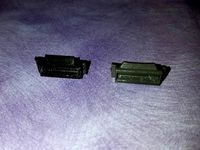
Cisco 8841 Retention Tab by Brizzle
...lost the retention tab for the handset and cisco does not list the part for replacement, so naturally i designed and printed one.
thingiverse
free

Bed Thumbwheel with M3 retention by BoothyBoothy
...bed thumbwheel with m3 retention by boothyboothy
thingiverse
yet another thumb wheel for a m3 bolt.
Sigma
3ddd
$1
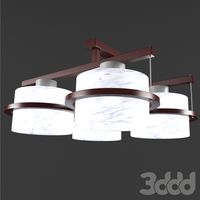
Sigma
...sigma
3ddd
sigma l2
люстра sigma
3ddd
$1
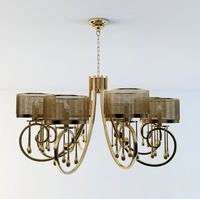
Sigma
...sigma
3ddd
sigma
люстра sigma l2 7117/8
3ddd
$1
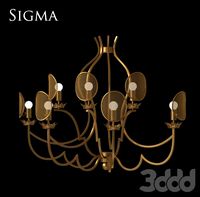
Бра Sigma
...бра sigma
3ddd
sigma
sigma
3ddd
$1
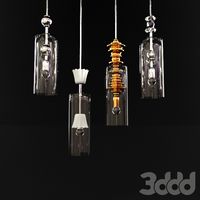
Sigma L2
...sigma l2
3ddd
sigma , sigma elle due
подвесы sigma l2
3ddd
$1
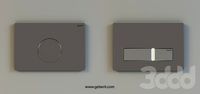
Geberit Sigma 10, Sigma 50
... sigma , кнопка слива
ультразамечательнейшие клавиши смыва geberit sigma 10 и sigma 50
3ddd
free
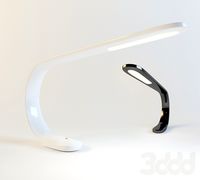
Vibia Sigma
...vibia sigma
3ddd
sigma , vibia
настольный светильник vibia sigma
3ddd
$1
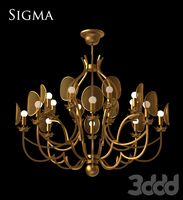
Люстра Sigma
...люстра sigma
3ddd
sigma
:)
3ddd
$1
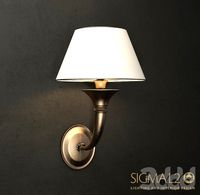
Sigma L2
...sigma l2
3ddd
sigma
sigma l2 z 187, 470*250 мм
3ddd
free
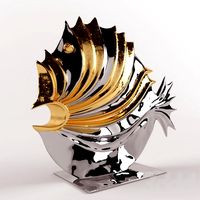
Sigma A 221
... regal , статуэтка
the regal collection. sigma.
3ddd
free

Sigma l2
...sigma l2
3ddd
sigma l2
настольная лампа. итальянской фабрики sigma l2. модель cl 1657.
Bowden
turbosquid
$199
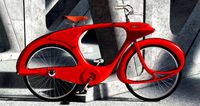
Vintage Ben Bowden Spacelander bike
... available on turbo squid, the world's leading provider of digital 3d models for visualization, films, television, and games.
3ddd
$1

Manooi Artica
...and pendants in various sizes and forms. suspension: galvanized bowden - dia. 1,5 mm. bulb: max 60 w -...
thingiverse
free
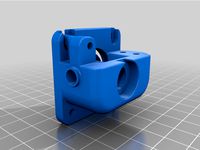
Remix Compact Bowden extruder - m6 bowden couplers and bowden tube pass-through
...ouplers and bowden tube pass-through
thingiverse
remix compact bowden extruder - m6 bowden couplers and bowden tube pass-through
thingiverse
free

Bowden Extruder
...bowden extruder
thingiverse
i have created bowden extruder for flsun delta 3d printer.
thingiverse
free

bowden 3mm by spee_D
...bowden 3mm by spee_d
thingiverse
for bowden 3mm
thingiverse
free

Bowden Tube Cutter
...bowden tube cutter
thingiverse
bowden tube cutter
thingiverse
free

Customizable Bowden Clip
...customizable bowden clip
thingiverse
customizable bowden clip
thingiverse
free
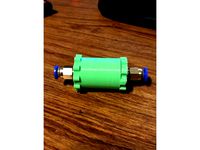
Bowden Oiler by fcheshire
...bowden oiler by fcheshire
thingiverse
inline bowden oiler
thingiverse
free

Bowden adapter by helkaroui
...bowden adapter by helkaroui
thingiverse
this is a fixed bowden adapter
thingiverse
free
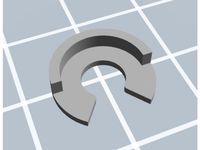
Adventure3 Bowden Clip
...adventure3 bowden clip
thingiverse
adventure3 bowden clip
Tube
archibase_planet
free
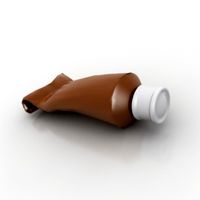
Tube
...tube
archibase planet
paint tube stationery
tube - 3d model (*.gsm+*.3ds) for interior 3d visualization.
turbosquid
free
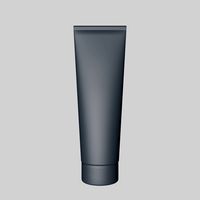
tube
...tube
turbosquid
free 3d model tube for download as c4d on turbosquid: 3d models for games, architecture, videos. (1378271)
archibase_planet
free
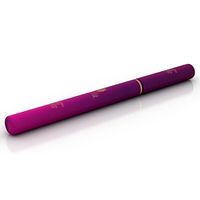
Tube
...tube
archibase planet
mascara cosmetics make-up
tube 1 - 3d model (*.gsm+*.3ds) for interior 3d visualization.
3d_export
$5

Tube pants
...tube pants
3dexport
tube pants
3d_export
free
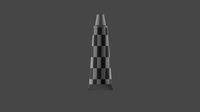
Tube
...tube
3dexport
turbosquid
free

TUBE
...
free 3d model tube for download as blend, dae, fbx, and obj on turbosquid: 3d models for games, architecture, videos. (1672199)
turbosquid
$29

tube
...lty free 3d model tube for download as 3ds, obj, c4d, and fbx on turbosquid: 3d models for games, architecture, videos. (1442047)
3ddd
$1
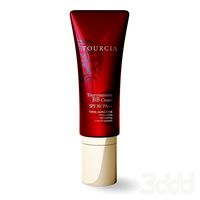
perfume tube
...perfume tube
3ddd
тюбик
perfume tube, тюбик
3ddd
$1
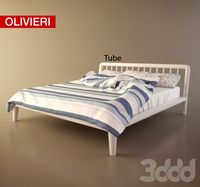
Olivieri Tube
...olivieri tube
3ddd
olivieri
кровать olivieri tube
turbosquid
$22
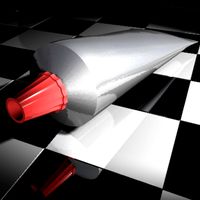
Tube
... available on turbo squid, the world's leading provider of digital 3d models for visualization, films, television, and games.
Fitting
turbosquid
$21
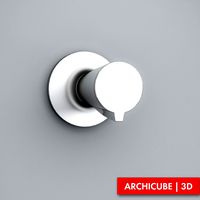
Fitting
... available on turbo squid, the world's leading provider of digital 3d models for visualization, films, television, and games.
turbosquid
$20

fitness
... available on turbo squid, the world's leading provider of digital 3d models for visualization, films, television, and games.
turbosquid
$5
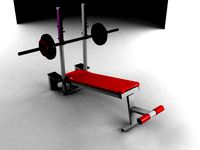
Fitness
... available on turbo squid, the world's leading provider of digital 3d models for visualization, films, television, and games.
turbosquid
$1
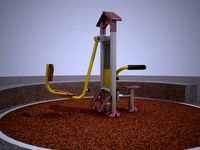
fitness
... available on turbo squid, the world's leading provider of digital 3d models for visualization, films, television, and games.
3d_export
$5

fittings
...fittings
3dexport
low poly 3d model for games
3d_export
$5

fittings
...fittings
3dexport
low poly 3d model for game
3d_export
$30
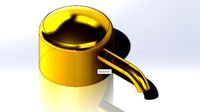
pipe fit
...pipe fit 3dexport this models basically used for pipe fitting ...
3d_ocean
$19
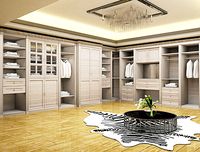
Fitting room
...m fitting fitting room furniture interior materials photorealistic restaurant table textured wardrobe
fitting room with textures.
turbosquid
free
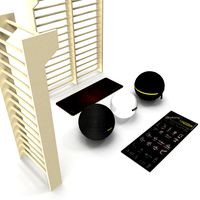
Fitness equipment, technogym tools, fitness ball
... available on turbo squid, the world's leading provider of digital 3d models for visualization, films, television, and games.
3ddd
$1
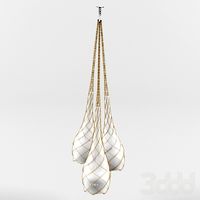
ITRE FIT
...itre fit
3ddd
itre
itre fit, моделировалась по фото. высота 800 мм, диаметр одного - 130 мм.