Thingiverse
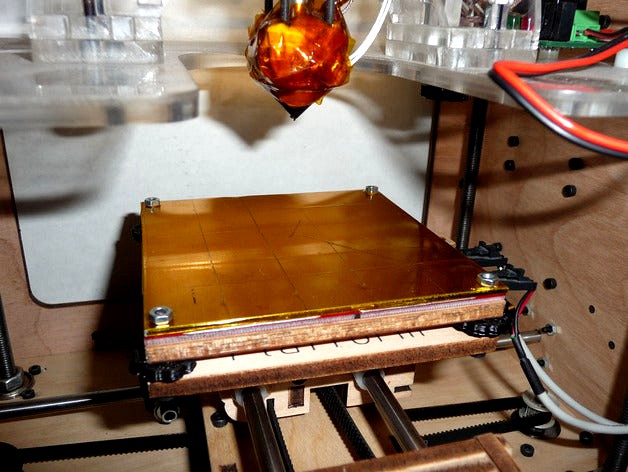
ABP to HBP in a few steps by eM5
by Thingiverse
Last crawled date: 3 years ago
Now new and improved! (Details at the end.)
I gave up on my Automatic Build Platform! (ABP)
I must admit that at the beginning we had some swell moments. Those graceful wipes at the start and the rolling off the belt at the end were memorable. But there was always something getting between us. Projects that would not stick or that would get knocked down mid-build half hour into the build. And in the rare moments when a raft-less object would finally finish it would have a wavy base. We tried making new belts, we tried kapon therapy and even going to different temperatures but nothing seemed to work. I could go on but it would seem petty on my part after our time together.
I know it seems cruel but I took it apart and built an HBP with some of its parts.
It was simple really. I took the heater board with the thermistor and connections from the ABP. I also removed the wooden base where the heater board sits because it has that nice round cutout that allow space for the connectors and the round hole in the center for the thermistor.
The three other pieces I used were:
the wooden base with the magnets of one of the two acrylic bases that came with my Ultimate Cupcake
a 100mm square sheet of zinc that I cut out of a piece that I had laying around in my garage. I used this since I did not want to put Kapon tape directly on the heater board in case I decide to reconcile with my ABP.
I needed slightly longer bolts so I used four M3 x 16mm bolts that I had left over from my original parts kit.
Now that it's put together I use the HBP profile for my g-code and my first build was beautiful. On the second or third build, the first layer was not sticking very well - making a bit of a mess of some of the detail. So I upped the base temperature to 135 and now it is doing a great job.
Projects stick nicely and don't curl on the base, and with the low and compact profile I no longer have the wobble I was getting on the ABP on tall builds.
Hopefully we can live happily ever after.
Well, we were not so happy. It turns out that my sheet of zink was not flat so there was as much as 1.5 mm difference from one place to another. So I went out and bough myself a piece of 2mm aluminum and had it cut to size. And I love it! It is perfectly flat and transfers heat beautifully. My next step is to inset the bolts so that the top is all flat.
I gave up on my Automatic Build Platform! (ABP)
I must admit that at the beginning we had some swell moments. Those graceful wipes at the start and the rolling off the belt at the end were memorable. But there was always something getting between us. Projects that would not stick or that would get knocked down mid-build half hour into the build. And in the rare moments when a raft-less object would finally finish it would have a wavy base. We tried making new belts, we tried kapon therapy and even going to different temperatures but nothing seemed to work. I could go on but it would seem petty on my part after our time together.
I know it seems cruel but I took it apart and built an HBP with some of its parts.
It was simple really. I took the heater board with the thermistor and connections from the ABP. I also removed the wooden base where the heater board sits because it has that nice round cutout that allow space for the connectors and the round hole in the center for the thermistor.
The three other pieces I used were:
the wooden base with the magnets of one of the two acrylic bases that came with my Ultimate Cupcake
a 100mm square sheet of zinc that I cut out of a piece that I had laying around in my garage. I used this since I did not want to put Kapon tape directly on the heater board in case I decide to reconcile with my ABP.
I needed slightly longer bolts so I used four M3 x 16mm bolts that I had left over from my original parts kit.
Now that it's put together I use the HBP profile for my g-code and my first build was beautiful. On the second or third build, the first layer was not sticking very well - making a bit of a mess of some of the detail. So I upped the base temperature to 135 and now it is doing a great job.
Projects stick nicely and don't curl on the base, and with the low and compact profile I no longer have the wobble I was getting on the ABP on tall builds.
Hopefully we can live happily ever after.
Well, we were not so happy. It turns out that my sheet of zink was not flat so there was as much as 1.5 mm difference from one place to another. So I went out and bough myself a piece of 2mm aluminum and had it cut to size. And I love it! It is perfectly flat and transfers heat beautifully. My next step is to inset the bolts so that the top is all flat.
Similar models
thingiverse
free
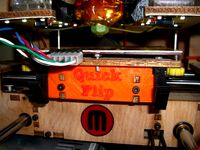
Quick Flip - fast swicth between HBP and ABP by Bluemetal
...to moves. i will post this one when i am done building and testing it.
i have added the sketchup files for your editing pleasure.
thingiverse
free

Replicator Platform Heater PCB by garyacrowellsr
...ng else that is resulting in poor contact.
this thing, uses the rear center hole of this hbp in a 3-point leveling arrangement.
thingiverse
free
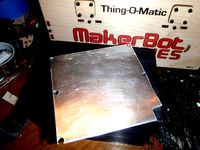
Veruca ABP Modification by WiggyG
...at a time
-requires the use of acetone; you must use proper ventilation/safety precautions with acetone to prevent fire/explosion
thingiverse
free
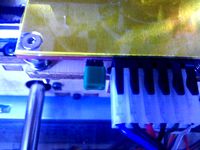
Dummy Jumper by dreameredeemer
...estion here http://softsolder.com/2011/04/15/thing-o-matic-protect-the-abp-motor-terminals-on-an-hbp/ and printed a dummy jumper.
thingiverse
free
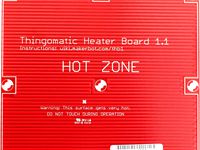
Thingomatic Heater Board v1.1 by MakerBot
...not least, the pcb includes a header for connecting it to the rest of the makerbot electronics so that you can easily wire it up.
thingiverse
free

Razer Tartarus Pro Phone Stand Attachment by bot_jonah
...od would require new (longer) screws. right now, i just have it attached with double-stick tape and that seems to work perfectly.
thingiverse
free

CTC Heated Build Platform Thermistor Fix by slippyr4
...istor. which is absolutely tiny, but works very well. you should be able to find one on rs, digikey, farnell, the usual suspects.
thingiverse
free

Automated Heated Build Platform by Laydas
...m by laydas
thingiverse
turn the thingomatic with a hbp into an automated printing machine as if it had an abp for no extra cost
thingiverse
free
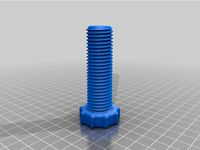
Even Longer Clamp Base - Bolt
...nd had a bolt that was too small for my use. this is just a longer version of the "clamp base - bolt" by justinspanier.
thingiverse
free

Martian 2 - Runcam Split mount by joeostrander
...s the board directly behind the camera with 4 m3 bolts. i've flown it several times now and it seems to be working dandy. :)
Em5
3d_export
$149

Olympus OM-D E-M5 Black 3D Model
...e-m5 black 3d model 3dexport black camera digital e-m5 em5 grip lens m5 olympus om-d om omd photo photography...
3d_export
$149

Olympus OM-D E-M5 Silver 3D Model
...om-d e-m5 silver 3d model 3dexport camera digital e-m5 em5 grip lens m5 olympus om-d om omd photo photography...
thingiverse
free

Leia Key Rings by eM5
...rt stuck together but i made a variation with my dog leia instead of the makerbot. she likes to say hello by climbing on my side.
thingiverse
free

Earring Tree by eM5
...arrings of different sizes.
now everyone is happy.
i've just made the base taller so that the earrings would not hang so low.
thingiverse
free
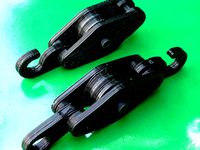
Block and Tackle - Pulleys by eM5
...ly. i also used a single 3mm x 22 cap screw in the center to fasten it together.
i've now added the half-sheave as requested.
thingiverse
free
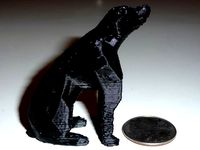
Leia 3D by eM5
...uess there is a way to cut down on those. in the end they cleaned up pretty well and they provided some support during the build.
thingiverse
free
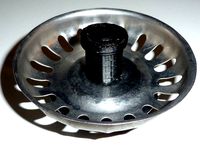
Sink plug knob by eM5
...lem that i'm not sure how to deal with.)
i used a glue gun to glue it on and now we have a nice little knob on our sink plug.
thingiverse
free

Block and Tackle Pulleys 2.0 by eM5
...t the lock is not locking properly. i'm in search of a cotton rope for a test, if it fails i'll have to re-work the lock.
thingiverse
free

Not-Stereo iPhone Dock by eM5
...e iphone is not stereo so i've uploaded a version for the iphone4 with only one horn. i have not made one but it should work.
thingiverse
free

Business Card Holder with Top by eM5
... cut-out design that i was not able to build, (buinesscardbox-3.stl), maybe some of you will have better luck (or skill) than me.
Hbp
thingiverse
free

HBP Wire Guide by jetty
...this derivative has one improvement over it's ancestor, an anti-twist bar to prevent the hbp guide from moving left to right.
thingiverse
free

HBP Cable Guide by Jamesdavid
...ring a long build. i designed this to solve that problem. it can probably be improved but it has worked well for the last week.
thingiverse
free
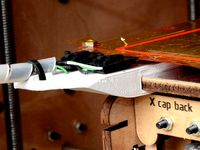
Strain relief, cupcake, HBP by ModelStation
...strain relief, cupcake, hbp by modelstation
thingiverse
this is a printable strain relief for a cupcake's hbp.
thingiverse
free
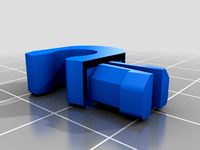
Extra Thick HBP Harness Clip by benmccal
...extra thick hbp harness clip by benmccal
thingiverse
this is a replacement cable clip for the extra thick hbp harness.
thingiverse
free

HBP Cable clip by merlinjim
...ng this modification - so ymmv. i anticipate there might be issues with it smacking into the bot housing at the y- / y+ extreme.
thingiverse
free
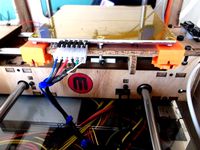
HBP Adjusters by epideath
...n the rear. if you put corner ones in the rear they may hit the z rods, or any extensions such as jetguys brass tube z extenders.
thingiverse
free

Strain Relief, Thing-O-Matic, HBP by ModelStation
...strain relief, thing-o-matic, hbp by modelstation
thingiverse
this is a printable strain relief for a thing-o-matic hbp.
thingiverse
free

Replicator HBP Washer Constraints by GeraldO
...ote it seems that newer replicators are shipping without these washers under the springs making this system unnecessary. awesome!
thingiverse
free
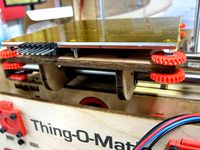
HBP Quick Leveler Redux by
...he thumbscrews alone greatly improve the tom's out of the box leveling setup.
simple!
this setup is working very well for me.
thingiverse
free

Makerbot Replicator 2/2X Cable grommet plug HBP by GILLESBOENISCH
...kerbot replicator 2/2x cable grommet plug hbp by gillesboenisch
thingiverse
makerbot replicator 2/2x grommet plug for hbp cable.
Abp
3dfindit
free
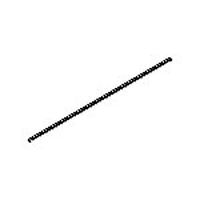
ABP
...abp
3dfind.it
catalog: festo
3dfindit
free

ABP
...abp
3dfind.it
catalog: festo
thingiverse
free
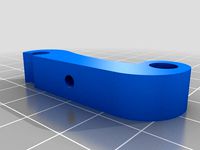
ABP belt tensioner arm for removable ABP mod by MarcusWolschon
...se
designed a shorter arm for the
abp belt tensioner, so it fits the different bolt-location when the removable abp mod is used.
3dfindit
free

SP10-ABP
...sp10-abp
3dfind.it
catalog: weidemann hydraulik
thingiverse
free

TOM ABP Side Replacement by skywurz
...tom abp side replacement by skywurz
thingiverse
tom (thing-o-matic) abp (automated build platform) replacement side
thingiverse
free
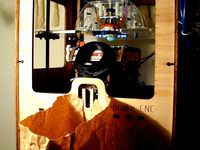
Paper bag catcher for makerbot ABP by natko
...paper bag catcher for makerbot abp by natko
thingiverse
its a paper bag catcher for abp
thingiverse
free
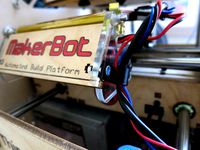
ABP wire clip by tomlombardi
...ep the abp wiring harness from flailing around. this thing allows you to quickly secure or remove the wiring harness to your abp.
thingiverse
free
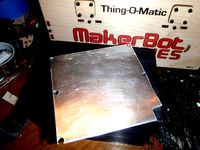
Veruca ABP Modification by WiggyG
...at a time
-requires the use of acetone; you must use proper ventilation/safety precautions with acetone to prevent fire/explosion
thingiverse
free
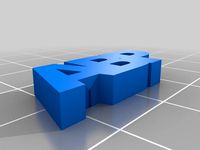
Smykke med bogstaver ABP by Stolpepost
...smykke med bogstaver abp by stolpepost
thingiverse
mange seje tin xd
thingiverse
free

Thing-O-Matic ABP Bushing Holder by niloc
...ic abp bushing holder by niloc
thingiverse
i broke this piece on my abp for my thing-o-matic while trying to remove the bushing.
Steps
3ddd
free
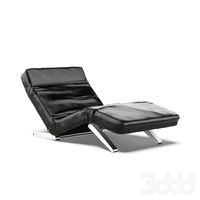
Pro Seda Step by Step
... by step
3ddd
step , proseda , кушетка
pro seda
design_connected
$9

Step
...step
designconnected
porada step coffee tables computer generated 3d model. designed by tarciso colzani.
turbosquid
$49

Steps
... available on turbo squid, the world's leading provider of digital 3d models for visualization, films, television, and games.
turbosquid
$30
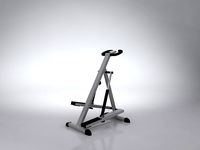
step
... available on turbo squid, the world's leading provider of digital 3d models for visualization, films, television, and games.
turbosquid
$11
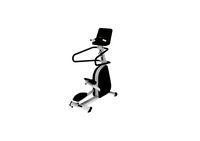
Step
... available on turbo squid, the world's leading provider of digital 3d models for visualization, films, television, and games.
3d_export
$20
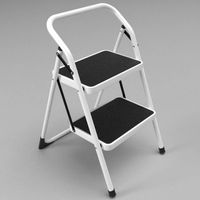
Folding steps step stool 3D Model
...tool stepstool steps ladder tool tools garage workshop shed basement
folding steps step stool 3d model pixelblock 43270 3dexport
3d_export
$5
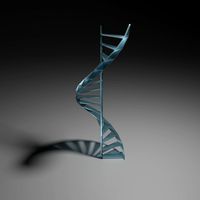
Glass steps
...glass steps
3dexport
well, just glass steps
3ddd
$1

Lago Steps
...lago steps
3ddd
lago
lago steps chair.
3d_export
$10
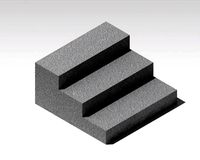
steps with cocrete
...steps with cocrete
3dexport
design steps for the architecture engineering purpose
archibase_planet
free
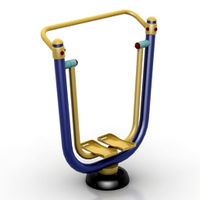
Rack step
...rack step
archibase planet
rack step rack gym
rack step - 3d model (*.gsm+*.3ds) for exterior 3d visualization.
Few
3d_export
free

ax few polygons
...ax few polygons
3dexport
few polygons ax created by me
turbosquid
free
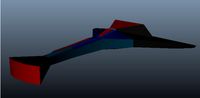
is a spaceship few resource
... available on turbo squid, the world's leading provider of digital 3d models for visualization, films, television, and games.
3d_export
$5
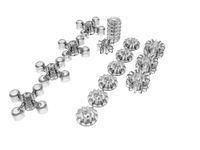
Few Lego gears 3D Model
...few lego gears 3d model
3dexport
lego gears technic
few lego gears 3d model edvarts 58648 3dexport
3d_export
$10
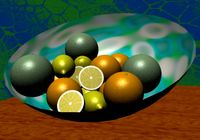
Few kinds of fruits 3D Model
...few kinds of fruits 3d model
3dexport
fruits orange melon lemon mix basket
few kinds of fruits 3d model pumar 50901 3dexport
3d_export
$20

Cancer
...cancer 3dexport river cancer 3d model for 3d printing few ...
3d_export
$5

dagger daga punhal
...dagger daga punhal 3dexport dagger in obj with few polygons and a high precision in...
3d_export
$5

tv table
...tv table 3dexport tv table contains a few books, two speakers. it will beautifuly fill in any...
3d_export
$5
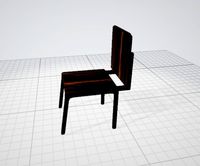
wooden-metal school chair
...chair 3dexport wooden-metal school chair . good quality model, few ...
3d_export
free

3dtext
...from 1-0 upper and lower case letters and a few special...
3d_export
$60
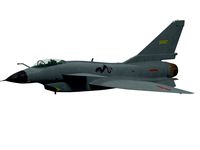
chengdu j-10 c vigorous dragon
...improved version of j-10a, with new electronica and a few external...