Thingiverse
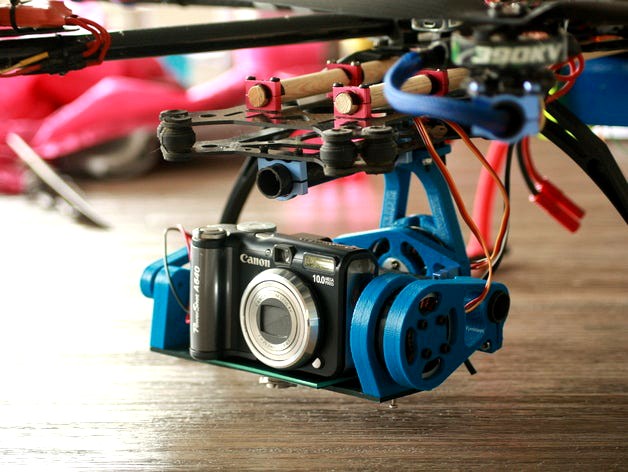
2-axis gimbal for mid-size camera by reneke
by Thingiverse
Last crawled date: 4 years ago
I made this gimbal for my Canon A640, but it can easily be used for other camera types. The design is based on the Nex5 gimbal from Nilsepils94 (http://www.thingiverse.com/thing:248930)
Total print volume is 98 cm3.
To complete the gimbal you will need:
2x Quanum 4008 brushless motors
1x controller board, 2-axis
1x carbon shock absorbing plate with rubber dampers
4x 16 mm alu. Tarot tube clamp
4x 12 mm tube clamp
...some srews and bolts
Update: first test with Sony NEX 5: http://youtu.be/yjy8nDaOKOk
update 2015-02-15:
I had problems with the gimbal when using it with the heavier Sony Nex. Sad to say I replaced it with it a DYS because of vibrations I could not get rid of. Probably because the construction is not stiff enough and I used too light rubber vibration dampers.
Update 2016-01-19:
with some more experience with the Alexmos in retrospect I think the vibrations were caused by bad PID values or bad connection of the IMU sensor.
For controller, a stand alone nulled version Alexmoss controller was used
Some small faults in the 3D print design:
diameter around motors of the could be 0.5 mm bigger (tight fit; had to use aceton)
cable location differ 90 degrees on some Quanum motors; The position seems not consistant in respect of the mounting thread holes
The design was printed with a Leapfrog, without support material.
More footage:http://youtu.be/FselVdqGLIA (stabilised)https://plus.google.com/photos/108394968200012243536/albums/6053086198104189761?authkey=CKeMrr-c9LfGAQ
Total print volume is 98 cm3.
To complete the gimbal you will need:
2x Quanum 4008 brushless motors
1x controller board, 2-axis
1x carbon shock absorbing plate with rubber dampers
4x 16 mm alu. Tarot tube clamp
4x 12 mm tube clamp
...some srews and bolts
Update: first test with Sony NEX 5: http://youtu.be/yjy8nDaOKOk
update 2015-02-15:
I had problems with the gimbal when using it with the heavier Sony Nex. Sad to say I replaced it with it a DYS because of vibrations I could not get rid of. Probably because the construction is not stiff enough and I used too light rubber vibration dampers.
Update 2016-01-19:
with some more experience with the Alexmos in retrospect I think the vibrations were caused by bad PID values or bad connection of the IMU sensor.
For controller, a stand alone nulled version Alexmoss controller was used
Some small faults in the 3D print design:
diameter around motors of the could be 0.5 mm bigger (tight fit; had to use aceton)
cable location differ 90 degrees on some Quanum motors; The position seems not consistant in respect of the mounting thread holes
The design was printed with a Leapfrog, without support material.
More footage:http://youtu.be/FselVdqGLIA (stabilised)https://plus.google.com/photos/108394968200012243536/albums/6053086198104189761?authkey=CKeMrr-c9LfGAQ